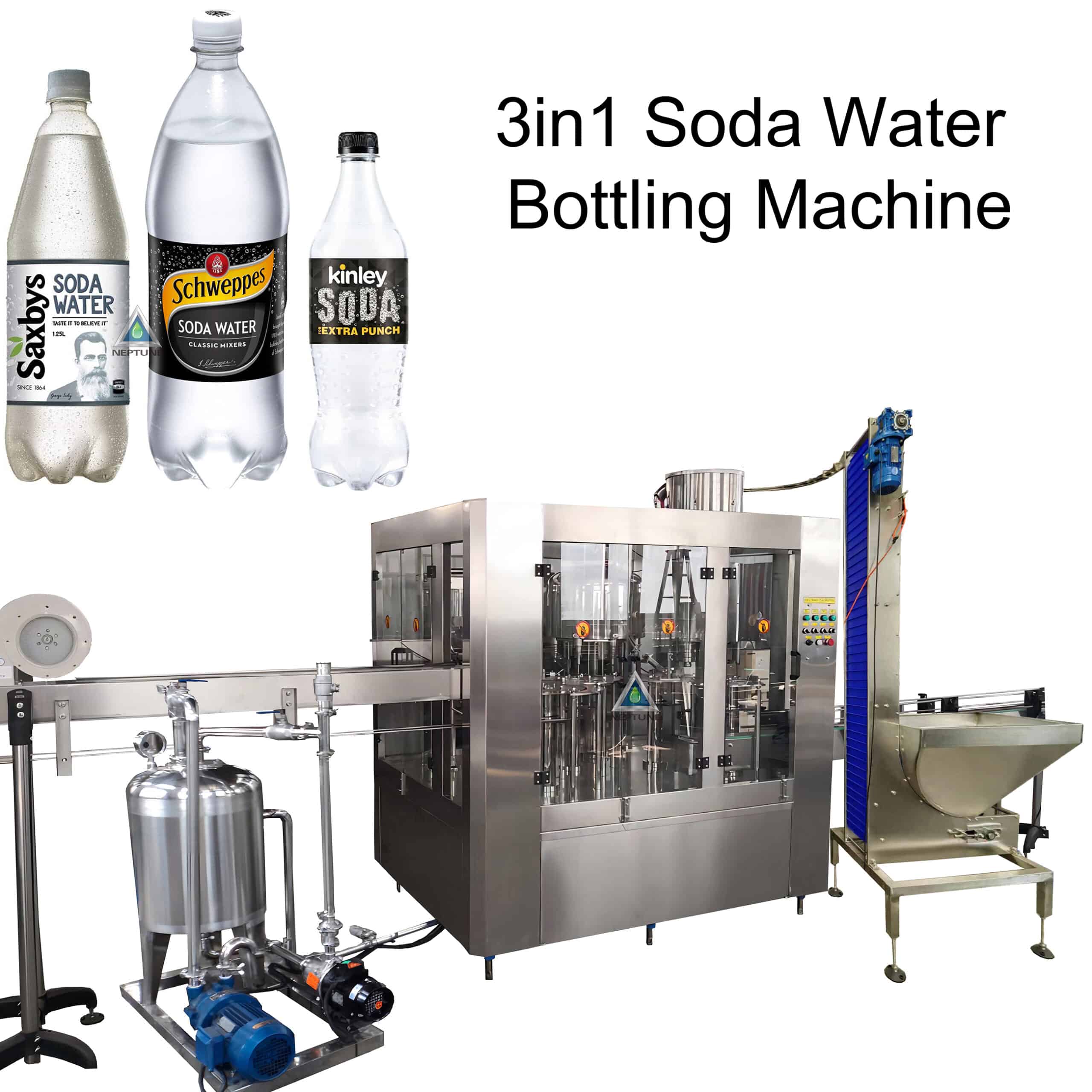
fOB PRICE $ 16000
The Soda Water Bottling Machine is a reliable and efficient solution for businesses engaged in the production of carbonated beverages, offering convenience, precision, and versatility in bottling processes.
MODEL | NCF 8-8-3 |
Production Capacity | 2000-2500 bottles/h |
Washing Head Quantity | 8 |
Filling Valve Quantity | 8 |
Capping Head Quantity | 3 |
Filling Temperature | 2℃~5℃; |
Filling Type | Balanced Pressure Filling |
Main Motor Power | 3 KW |
Bottle diameter | 40-70mm |
Bottle height | 130-260mm |
Air resource pressure | 0.5Mpa |
Filling Beverage | 1 T/H |
Consume Water | 0.8T/H |
Control Type | PLC |
Central Diameter of Filling Valve | ¢320mm |
Central Diameter of Capping Machine | ¢120mm |
Central Diameter of Washing Machine | ¢320mm |
Dimension | 1850 X 1450X2000mm |
Net Weight: | 1300kg |
Soda Water Bottling Machine is an all-in-one solution that seamlessly integrates rinser, filler, and capper functions into a single machine. Utilizing advanced balance pressure filling technology, this machine is specifically designed for the production of soda water and sparkling water.
Key Features:
- All-in-One Design:
- The machine combines the rinsing, filling, and capping processes within a single unit, streamlining the production line.
- Balance Pressure Filling Technology:
- Incorporates advanced balance pressure filling technology for precise and efficient filling of soda water and sparkling water.
- Versatile Application:
- Specifically designed to handle the unique requirements of carbonated beverages, making it ideal for soda water production.
- Efficient Rinsing Function:
- The rinser function ensures thorough cleaning of bottles before the filling process, maintaining hygiene standards.
- Accurate Filling:
- Utilizes precise filling mechanisms to maintain the correct carbonation levels in each bottle.
- Capping System:
- Equipped with a capping mechanism to securely seal bottles, preventing gas leakage and maintaining the carbonation of the beverage.
- User-Friendly Operation:
- Designed for ease of use with user-friendly controls, allowing operators to efficiently manage the production process.
- High-Quality Materials:
- Constructed with durable and food-grade materials to meet hygiene standards and ensure the quality of the bottled beverages.
- Customizable Settings:
- Adjustable settings to accommodate different bottle sizes and carbonation levels, providing flexibility in production.
- Production Efficiency:
- Optimized for high production efficiency, contributing to a smooth and continuous bottling process.
Applications:
- Ideal for bottling various carbonated beverages, including soda water and sparkling water.
Benefits:
- Reduces production complexity by consolidating multiple functions into a single machine.
- Ensures accurate and consistent carbonation levels for high-quality beverages.
- Enhances operational efficiency and streamlines the bottling process.
This Three-in-One unit stands as a testament to our commitment to innovation, combining the latest technologies and extensive production experience to deliver a versatile and efficient solution. It addresses the unique needs of the carbonated drink production sector while allowing for customization to meet the diverse demands of users.
Structural Characteristics
- Entering and Exit Bottle Type:
- Straight line configuration; bottles enter on the left side of the chain and exit on the right side.
- Rotational Direction:
- Clockwise rotation for each machine.
- Washing, Filling Pipeline:
- Liquid supply in the lower part of the structural design to meet sanitary requirements.
Sanitary Design:
- Material Selection:
- Filling cylinder, filling valve, and all parts in contact with materials are made of micro-carbon stainless steel.
- Micro-carbon stainless steel offers corrosion-proof characteristics and is easily washable.
- Work Table Design:
- Stainless steel-covered work table, strictly sealed to protect the driving device in the ground frame.
- Facilitates easy cleaning and maintenance.
Filling Quality:
- Filling Valve Efficiency:
- High-speed, high-quality filling valve ensures optimal filling quality.
- DCGF Type unit’s filling valve has a registered speed of 110ml/s, with no filling loss and no leakage in the exhaust pipe.
- Liquid Level Control:
- Correct control of liquid level in the bottle, with a height error not exceeding ±5mm based on the bottle neck diameter.
Capping Quality:
- Capping Mechanism:
- Magnetic screw capping with adjustable screwing cap moment to reduce cap damage and ensure tight seals.
Operation and Automation:
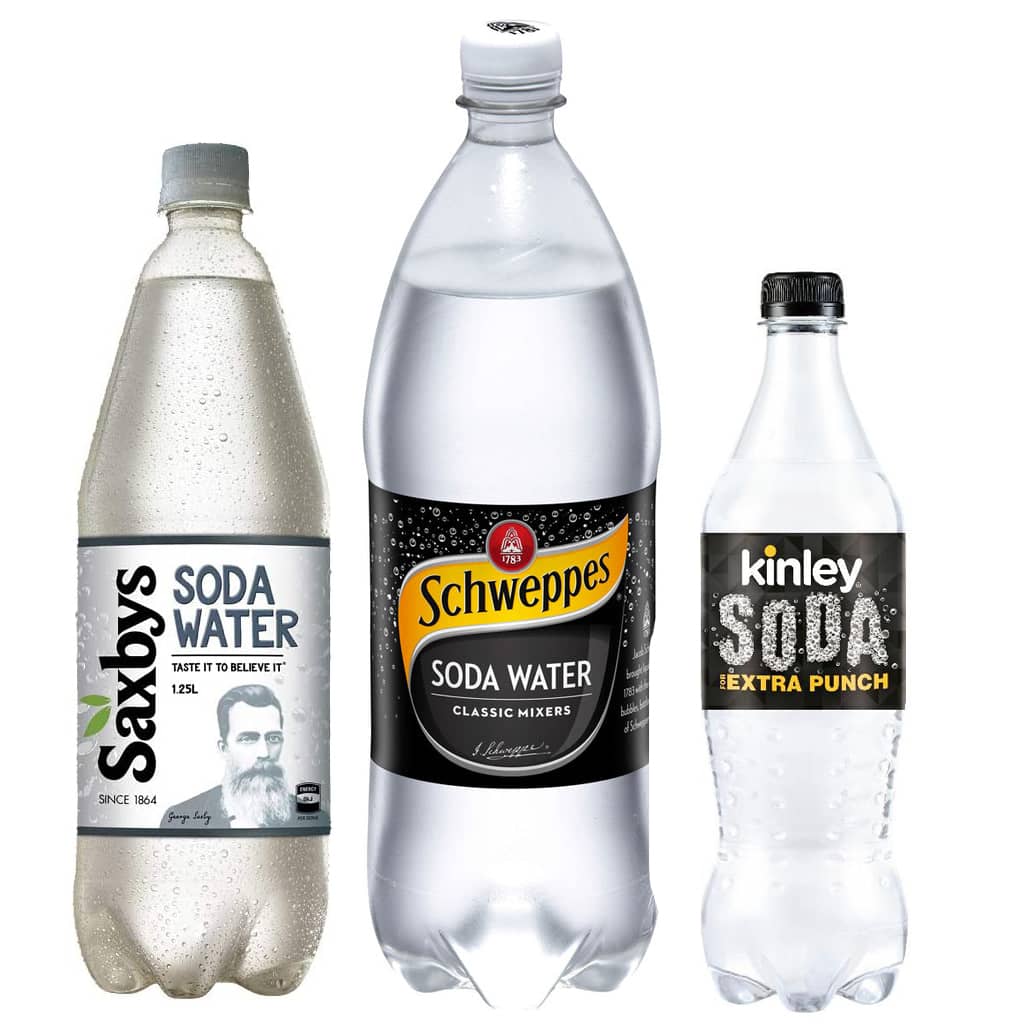
- Safety and Reliability:
- High level of automation with an auto control system and PLC programmable control.
- Frequency controller for convenient speed adjustment.
- Auto-stop protection in case of bottle blockage or wheel displacement, preventing machine damage.
- No-Bottle No-Fill System:
- Auto-stop if no bottle is detected on the line, and the filling valve closes if a broken bottle is identified.
- Run Stability:
- Bottle chain and material design ensure a steady supply of bottles.
- Stainless steel and engineering plastic components for the start wheel and bottle guide plate to ensure steady movement at high speed.
Main Configuration:
- Material:
- Filling valve and liquid tank made of 304 stainless steel.
- Main Motor:
- National brand.
- Sliding Bearing:
- Taiwan.
- Frequency Inverter:
- MITSUBISHI.
- Touch Screen:
- Taiwan.
- PLC:
- MITSUBISHI.
- Pneumatic Components:
- Airtac.
- Seals:
- National brand.
- Photocell Switch and Proximity Switch:
- Taiwan.
This DCGF Type unit is meticulously designed for efficient and reliable washing, filling, and capping processes, with a focus on quality, safety, and automation.