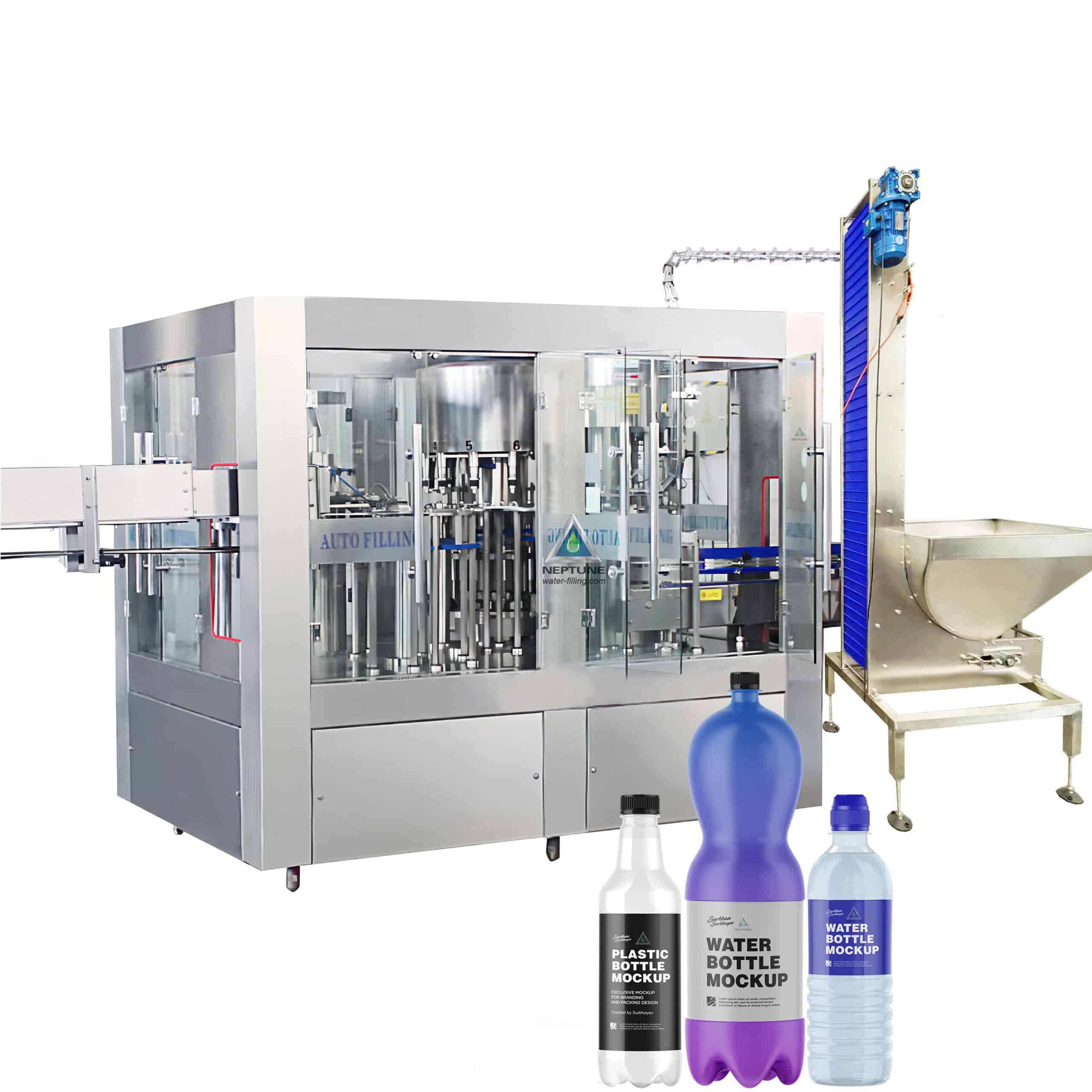
FOB PRICE $ 14930
What this price included?
NF 14-12-5 Washing-Filling-Capping (Three-in-One Unit) Machine, 1SET |
Light check, 1SET |
Cap automatic loading and feeding machine, 1SET |
2M Air conveyor,1psc air blower, 1SET |
2M conveyor,1psc motor, 1SET |
A 3-in-1 mineral water bottling machine is a type of equipment designed to perform three essential functions in the bottling process: washing, filling, and capping.
- Washing: The machine includes a washing section that cleans the bottles before filling. This process typically involves rinsing the bottles with a cleaning solution or sterilized water to remove any contaminants or impurities.
- Filling: After washing, the bottles move to the filling section where they are filled with mineral water. The machine is equipped with filling nozzles that accurately dispense the specified amount of water into each bottle.
- Capping: Once filled, the bottles proceed to the capping section where caps are placed and sealed on the bottles. This ensures the integrity and freshness of the mineral water inside.
3-in-1 Bottling mineral water machines are designed for efficiency and automation, streamlining the entire bottling process into a single, integrated system.It is commonly used in the production of mineral water and spring water, to ensure consistency and quality in the bottling operation.
what is cap automatic loading and feeding machine?
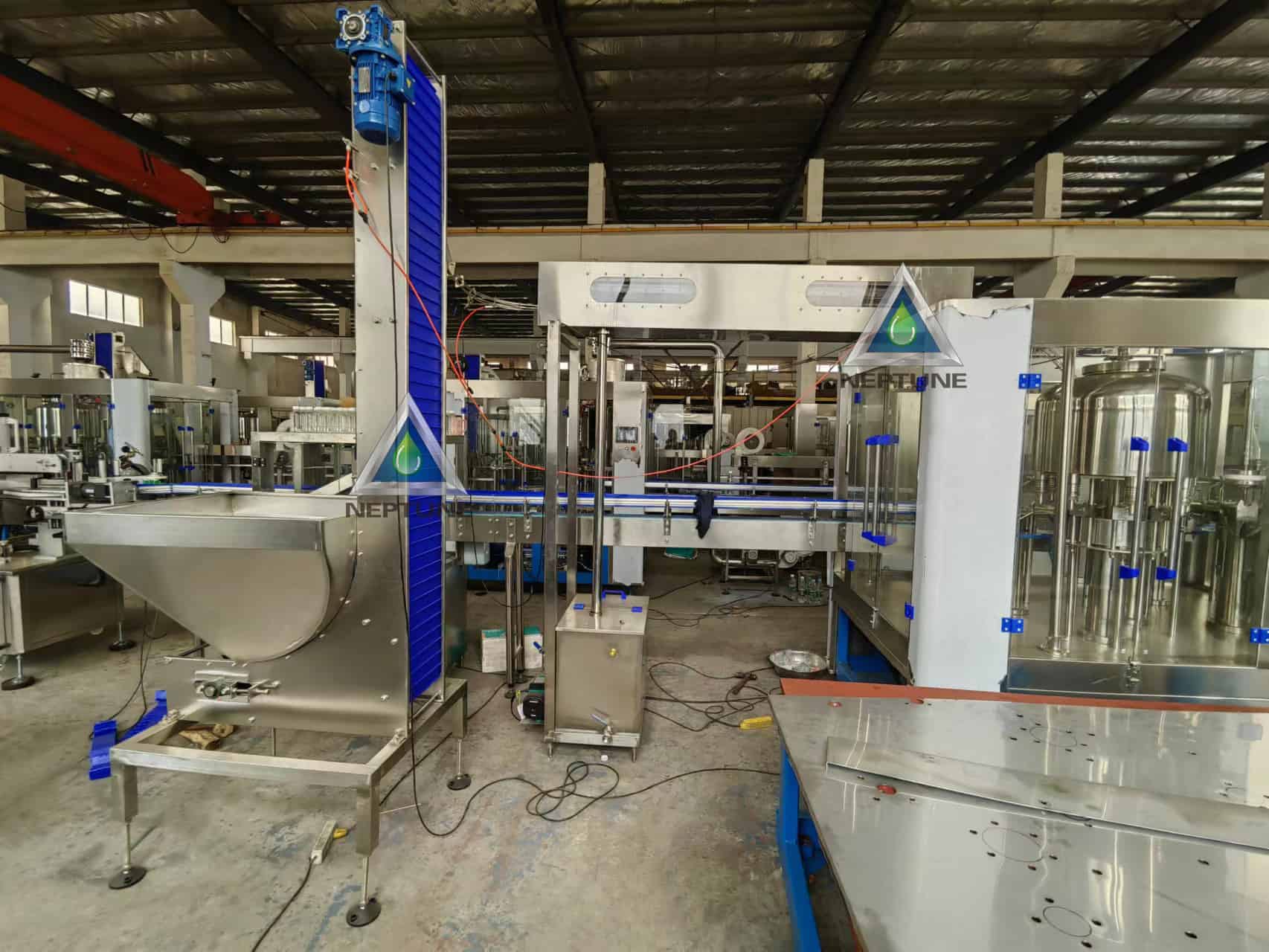
A cap automatic loading and feeding machine is a specialized equipment used in 3in1 water bottling machine to automate the process of loading and feeding caps onto bottles. This machine is designed to enhance efficiency and reduce manual labor.
How does the 3in1 machine work in the bottling process?
The 3in1 mineral water bottling machine is a versatile and efficient equipment that integrates three essential functions in the bottling process: washing, filling, and capping. Here’s a brief overview of how the 3in1 machine works:
Washing:
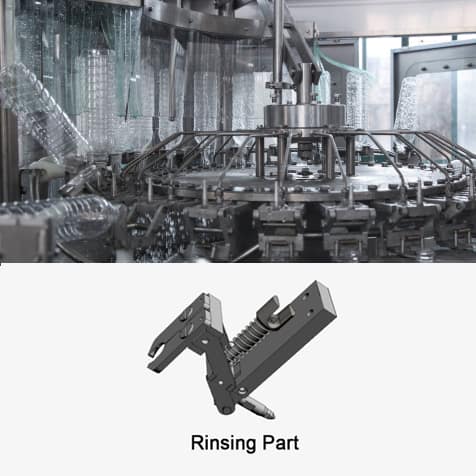
- Bottles are fed into the machine and are first subjected to a thorough washing process.
- High-pressure nozzles and brushes remove contaminants, residues, and impurities from the interior and exterior of the bottles.
- The washing process ensures that the bottles are clean and sanitized before filling.
Filling:
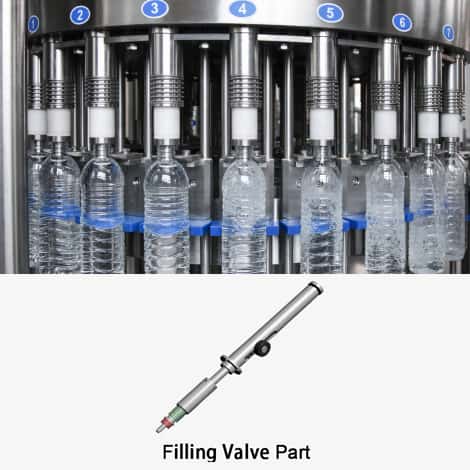
- Cleaned bottles move to the filling station, where they are precisely filled with the desired amount of mineral water.
- The filling process is typically controlled by a set of valves that open and close to allow the water to flow into the bottles.
- The filling level is accurately maintained to meet specific volume requirements.
Capping:
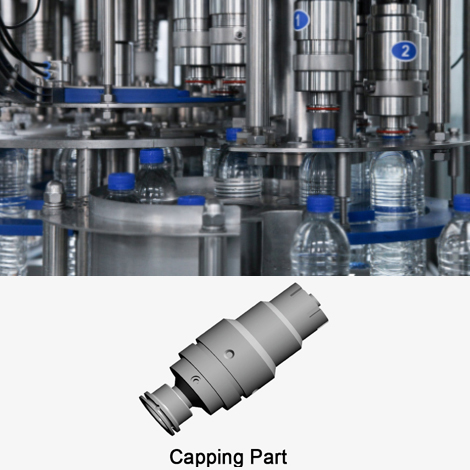
- After filling, the bottles proceed to the capping station.
- Caps are automatically loaded onto the bottles, and capping mechanisms securely seal the bottles to prevent any leakage.
- Different types of caps can be accommodated based on the machine’s design and customization.
The entire process is automated, ensuring a smooth and efficient operation. The 3in1 design minimizes the need for manual intervention and provides a compact solution for small to medium-scale mineral water bottling. The machine’s user-friendly interface allows operators to monitor and control the entire process easily.
Is the machine suitable for different bottle sizes and shapes?
Yes, NEPTUNE MACHINERY 3in1 mineral water bottling machines are designed to be adaptable to different bottle sizes and shapes. The 3in1 mineral water bottling machine is adjustable mechanisms, changeable molds, and flexible components that allow it to accommodate a variety of bottles. Here are some common aspects that contribute to their suitability for different bottle sizes and shapes:
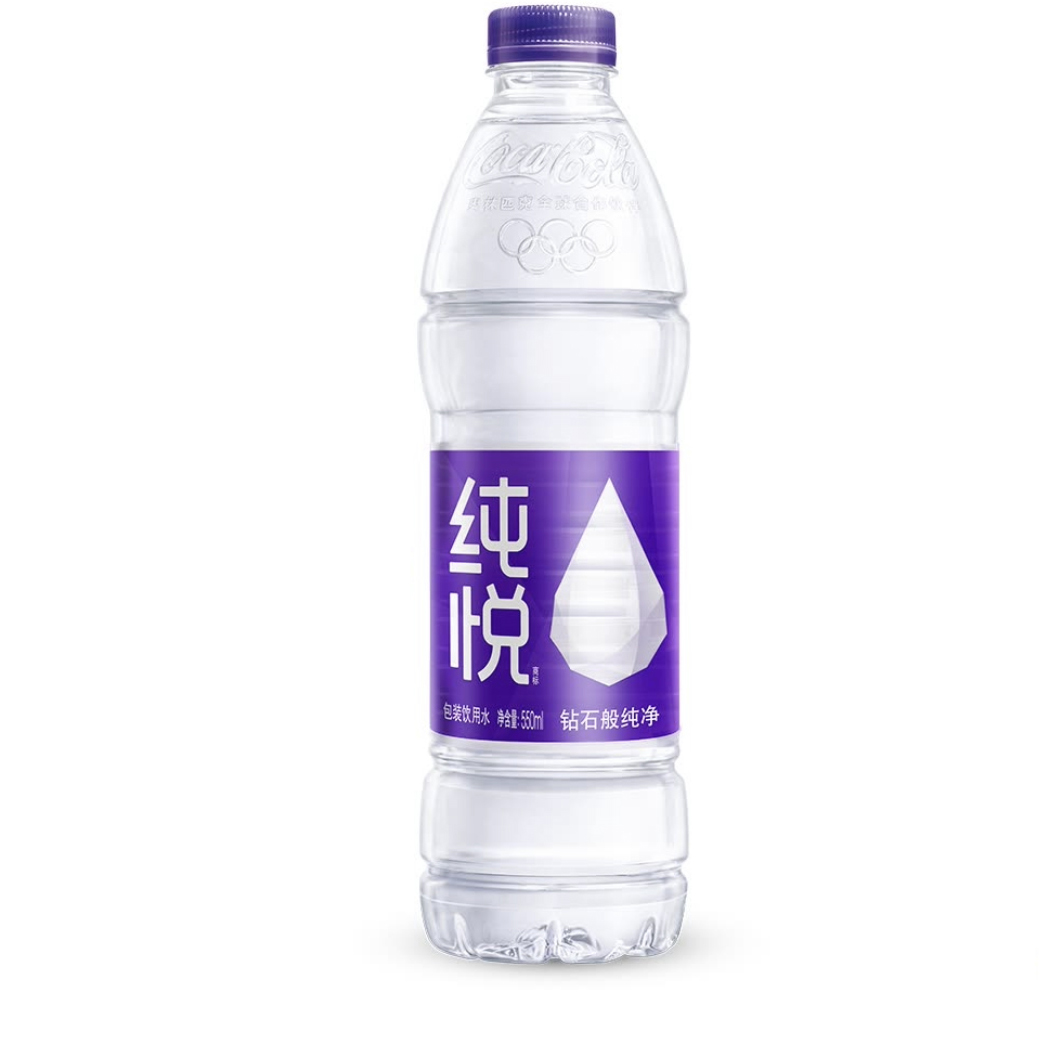
Production 4000 bottles per hour: depend on 500ml bottle water
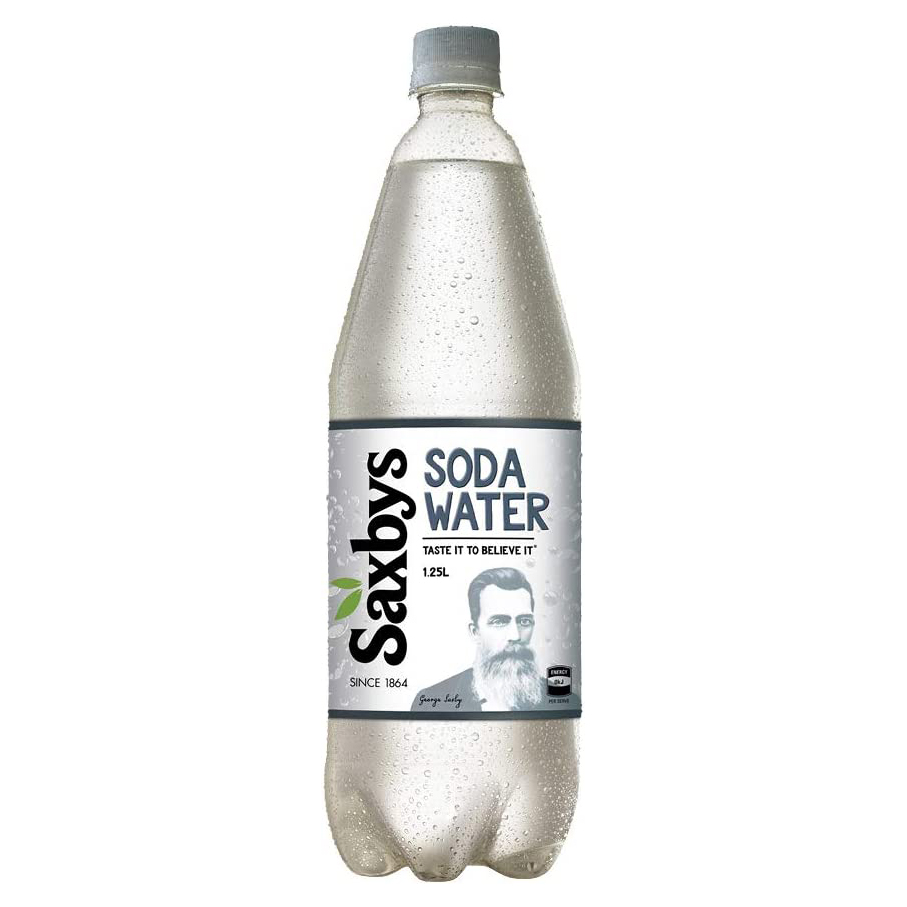
Production 3000 bottles per hour: depend on 1250ml bottle water
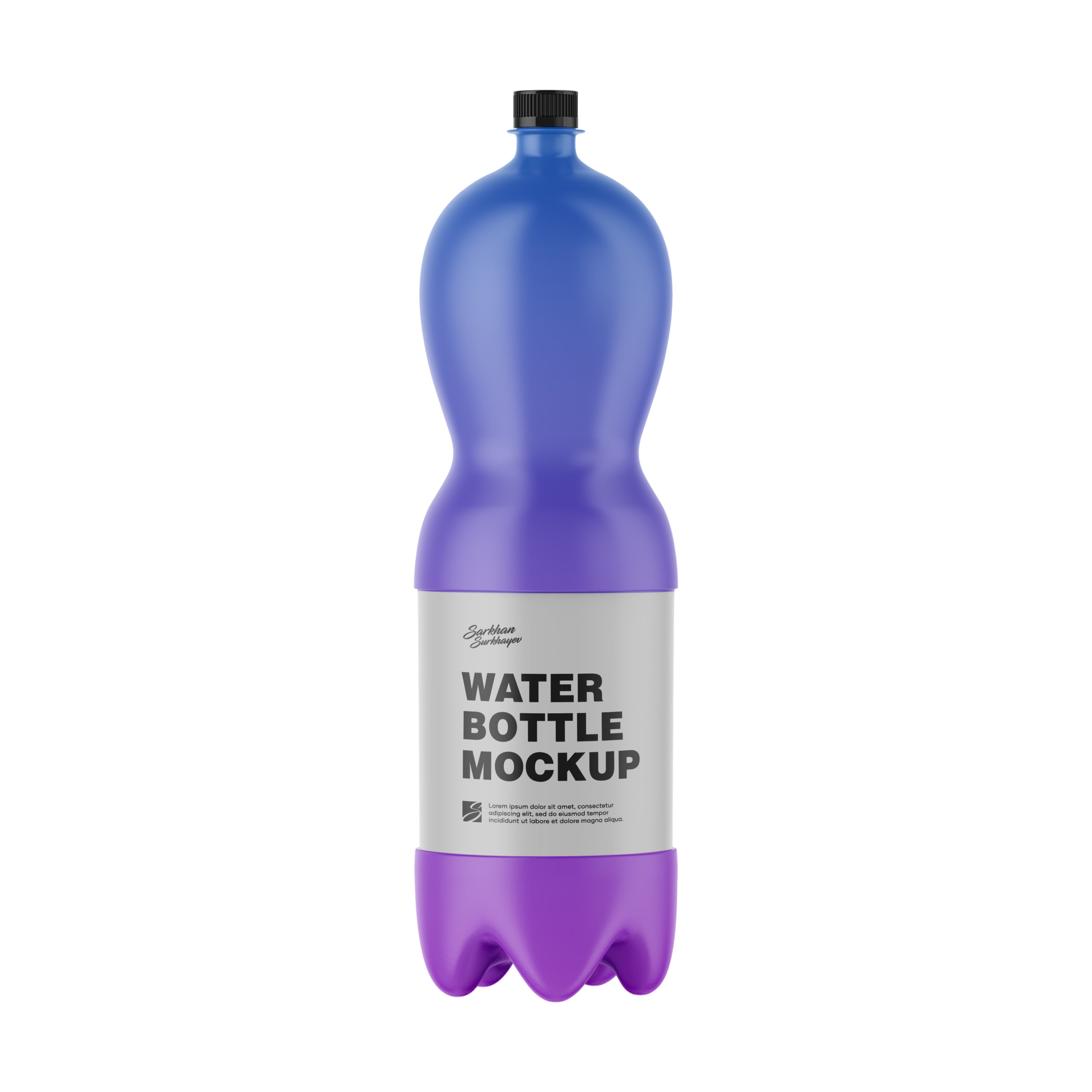
Production 2500 bottles per hour: depend on 1500ml bottle water
- Adjustable Guides and Conveyors:The conveyors and bottle guides in the machine can often be adjusted to accommodate bottles of varying sizes and shapes.
- Interchangeable Parts:Changeable molds and interchangeable parts enable the machine to handle different bottle shapes and sizes with ease.
- Variable Speed Controls:Variable speed controls for conveyors and filling mechanisms allow operators to adjust the production line to match the requirements of different bottles.
- Customizable Filling Heads:Some machines come with customizable filling heads that can be adapted to different bottle neck sizes and shapes.
- Modular Design:A modular design allows for easy integration of components suitable for specific bottle sizes, making the machine versatile.
- Quick Changeover:Machines designed for quick changeover between different bottle types facilitate efficiency when switching production runs.
- Adaptable Capping Systems:The capping systems are often designed to handle various cap sizes and types, ensuring compatibility with different bottles.
- Flexible Grippers or Clamps:Grippers or clamps that hold the bottles during the filling and capping process may be adjustable to accommodate different shapes.
Before selecting a 3in1 mineral water bottling machine, it’s essential to consider the range of bottle sizes and shapes you plan to produce.
Can it handle various types of caps for different bottles?
The 3in1 mineral water bottling machine to handle various types of caps for different bottles depends on its design and specifications.
- Cap Size and Type: Check the size and type of caps you intend to use. Ask neptune professional engineer for cap size and type confirm.
- The cap need fit the Cap Feeding Mechanism:
- Changeover Process: Evaluate the ease and efficiency of the changeover process for switching between different cap types. Quick and straightforward changeovers are beneficial for production flexibility.
- Customization Options: Inquire with the manufacturer about any customization options available to tailor the machine to your specific cap requirements. Some machines may offer flexibility through customization.
- Compatibility with Cap Sorters: If you use cap sorters or sorting systems as part of your production line, ensure that the 3in1 machine is compatible with these systems for seamless integration.
- Manufacturer Guidelines: Follow the manufacturer’s guidelines and recommendations regarding the types of caps the machine can handle. Adhering to these guidelines ensures optimal performance and longevity of the equipment.
It’s essential to communicate your specific cap requirements with the machine manufacturer to confirm whether the 3in1 bottling machine is suitable for the range of caps you intend to use. Additionally, proper training of operators on cap changeover procedures is crucial to maintaining efficiency during production transitions.
MODEL | 16-12-6 |
Production Capacity | 4000 Bottles per hour |
Washing Head Quantity | 16 |
Filling Valve Quantity | 12 |
Capping Head Quantity | 6 |
Filling Temperature | Normal temperature |
Filling Type | Constant Pressure Filling |
Main Motor Power | 2.2KW |
Ordering-Cap Motor Power | 0.09KW |
Cap Elevating Motor Power | 0.34KW |
Washing Pump Power | 0.37KW |
Liquid Inlet Pump Power | 0.55KW |
Consume Water | 1.2T/h ( Un-including drink water) |
Control Type | PLC |
Central Diameter of Filling Valve | 480mm |
Central Diameter of Capping Machine | 240mm |
Central Diameter of Washing Machine | 640mm |
Dimension | 2100 X 1500X2200mm |
Net Weight: | 3500kg |