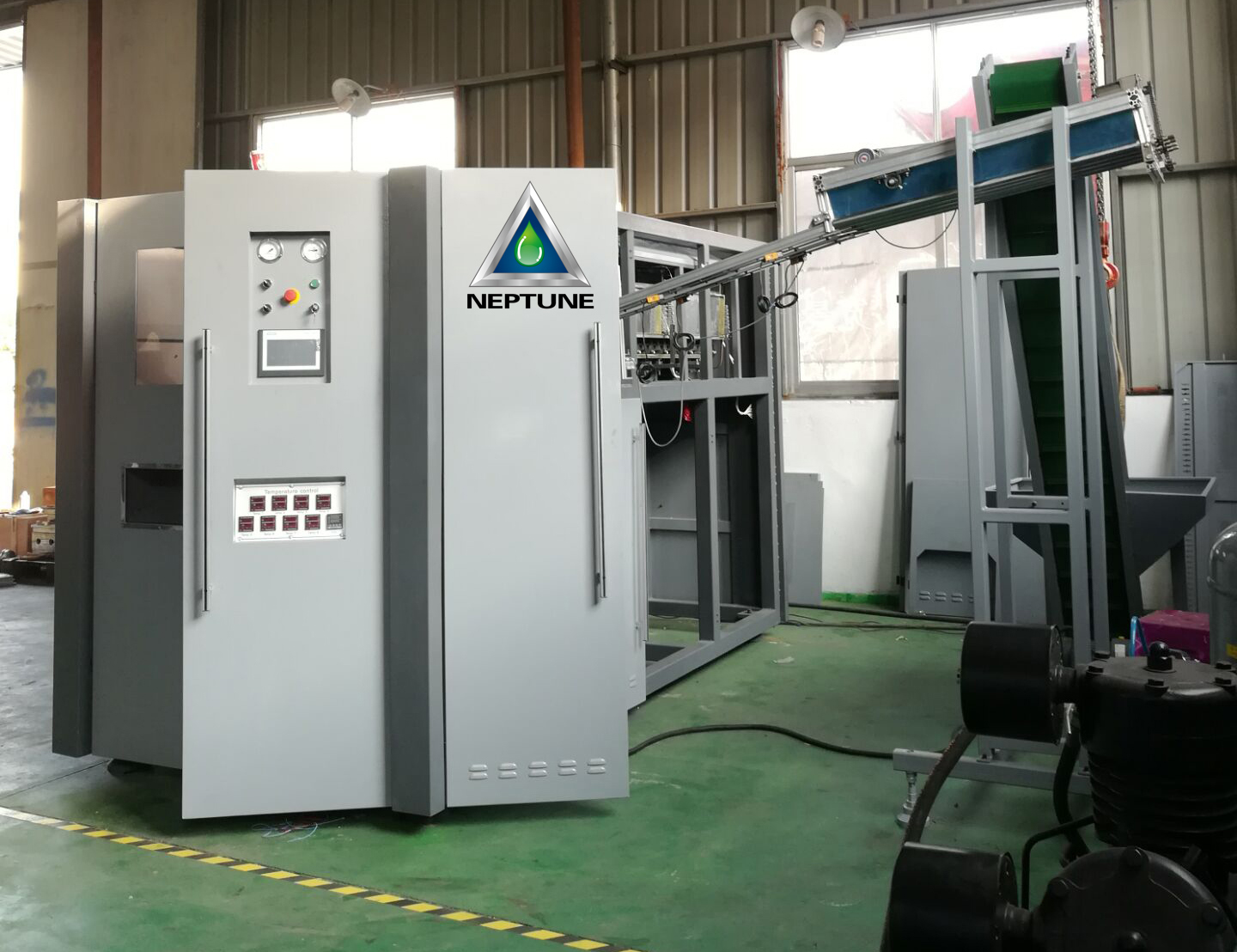
WHAT IS THIS 2000BPH AUTO BLOW MOLDING MACHINE COST:
fOB PRICE USD33240
What this price included?
NO | NAME | UNIT FOB PRICE | QC |
1 | BM-A2 Auto 2Cavity Blow Molding Machine | USD 15,000.00 | 1SET |
Automatic Preform Loading Unscrambler | USD 2,340.00 | 1SET | |
2 | 1.6m3/min 30Kg HP Air Compressor, Shangair Brand | USD 2,800.00 | 1SET |
3 | 1.6m3/min 10Kg LP Air Compressor, Shangair Brand | USD 1,550.00 | 1SET |
4 | Air Dryer 2.0 m3/min 30Kg | USD 650.00 | 1SET |
5 | Air filter 2.0 m3/min 30Kg | USD 500.00 | 2SET |
6 | Air Tank 0.6 m3/30Kg | USD 700.00 | 1SET |
7 | 3HP Blow Mold Air-Chiller | USD 1,350.00 | 1SET |
8 | Air tube & Spare parts | FREE | 1SET |
9 | Two cavity Blow Mold (250-2000ml) | USD 1,100.00 | 1SET |
Unleashing Precision in Bottle Manufacturing
NEPTUNE Machinery proudly introduces the 2000BPH Automatic PET Bottle Blow Molding Machine, a technological marvel designed to revolutionize the production of PET plastic water bottles. This cutting-edge machine combines user-friendly operation with exceptional quality, offering a seamless solution for your bottle manufacturing needs.
Key Features:
- Versatile Bottle Sizes: The machine caters to a range of bottle sizes, from 17oz, 20oz, 300ml, 0.5 liters, 1 liter, to 2 liters. This versatility allows you to produce a variety of bottles to meet diverse market demands.
- Efficient Production: With a capacity of 2000 bottles per hour, this automatic blow molding machine ensures efficient and high-speed production. It is ideal for manufacturing mineral water bottles, pure water bottles, and even bottles for juices and carbonated drinks.
- Adaptable Volume Range: The machine specializes in producing bottles with volumes ranging from 0.1L to 2L, offering flexibility in meeting different product packaging requirements.
- Easy Mold Change: Changing the mold and adjusting spare parts is a breeze, enabling swift transitions between different bottle shapes and sizes. This feature enhances operational efficiency and minimizes downtime.
- Precise PET Bottle Manufacturing: The machine is optimized for PET plastic, ensuring the production of high-quality and durable bottles. Its precision in molding guarantees consistent results with every cycle.
- Oversea Installation Support: NEPTUNE Machinery goes the extra mile by offering oversea installation support, ensuring that the machine is seamlessly integrated into your production setup.
Technical Specifications:
- Volume Range: 0.1L – 2L
- Production Capacity: 2000 Bottles Per Hour (BPH)
- Bottle Sizes: 17oz, 20oz, 300ml, 0.5L, 1L, 2L
- Material: PET Plastic
- Bottle Blowing Height: 50-350 mm
- Max. Mould Thickness: 240mm
- Machine Power Capacity: 25KW
- Voltage: 380V 3-phase / 220V 3-phase 50/60Hz
- Working Pressure: 0.7-0.9Mpa
- Blowing Pressure: 1.6-4.0Mpa
- Size Dimension: 1908mm(L) × 1280mm(W) × 1800mm(H)
Auxiliary equipment
Auxiliary equipment plays a crucial role in supporting the overall functioning of the PET bottle blow molding machine. Here’s an introduction to the functions of various auxiliary equipment:
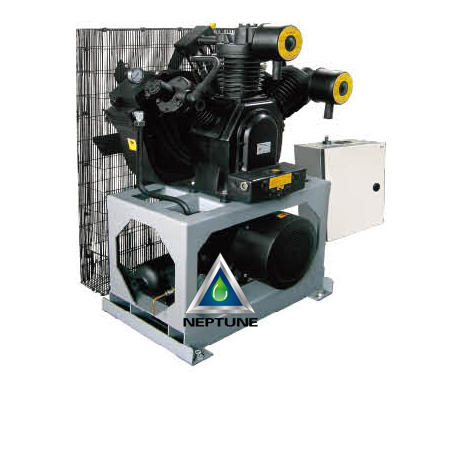
High-Pressure Air Compressor:
- Function: Provides high-pressure compressed air required for the blowing process.
- Importance: Essential for the expansion and shaping of PET preforms into bottles.
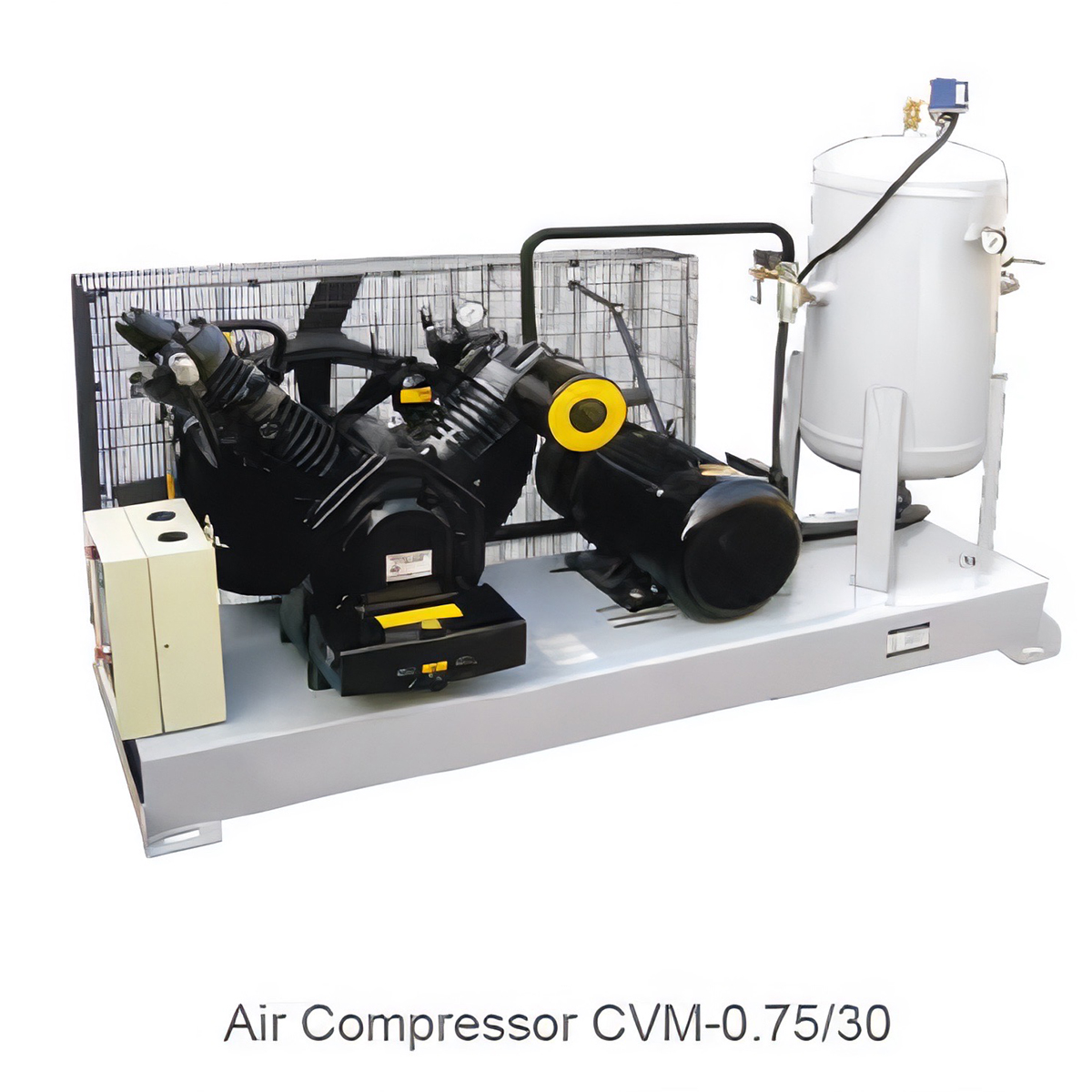
Low-Pressure Air Compressor:
- Function: Supplies low-pressure air for pneumatic components and control systems.
- Importance: Supports various machine functions and controls.
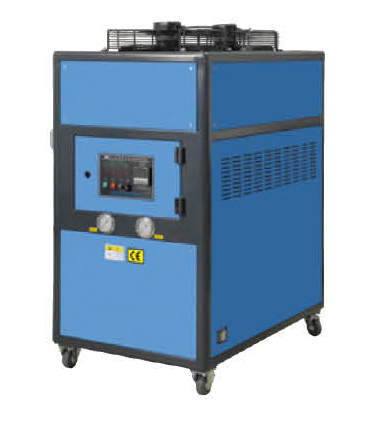
Mold Chiller:
- Function: Cools down the molds used in the blowing process.
- Importance: Maintains optimal temperature for the molds, preventing overheating and ensuring consistent bottle quality.
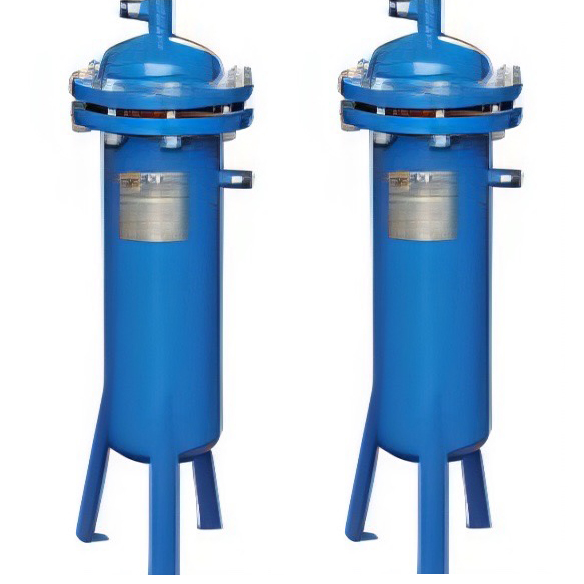
Air Filter:
- Function: Removes impurities, dust, and moisture from the compressed air.
- Importance: Ensures the quality of compressed air, preventing contamination of bottles during the blowing process.
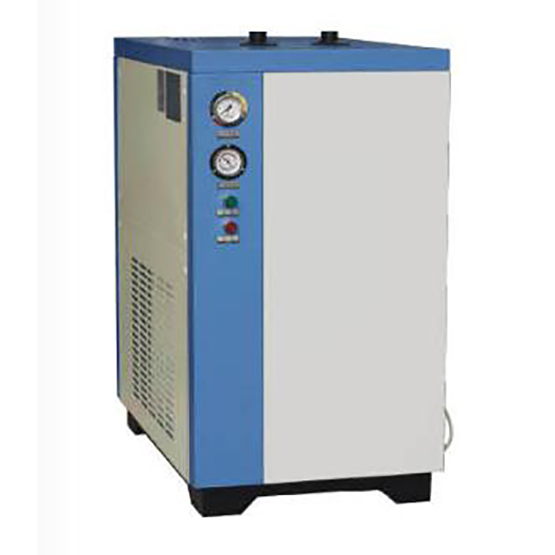
Air Dryer:
- Function: Removes moisture from the compressed air to prevent condensation.
- Importance: Moisture-free air is essential for maintaining product quality and preventing defects in the bottles.
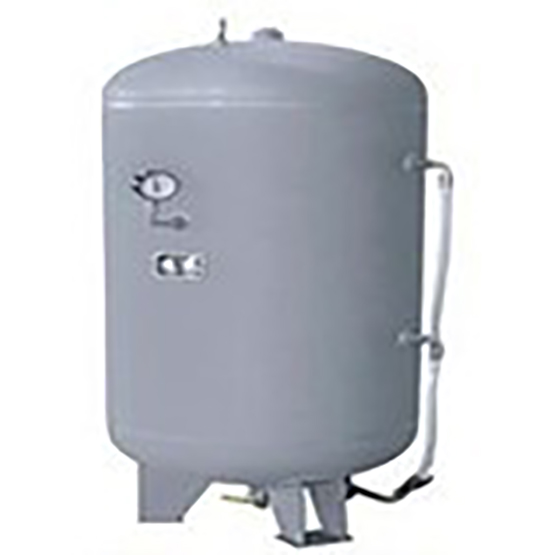
Air Tank:
- Function: Stores compressed air for immediate use when needed.
- Importance: Provides a reservoir of air to meet sudden demands, ensuring consistent machine performance.
What Types of Bottles Can be Produced?
220ml bottle
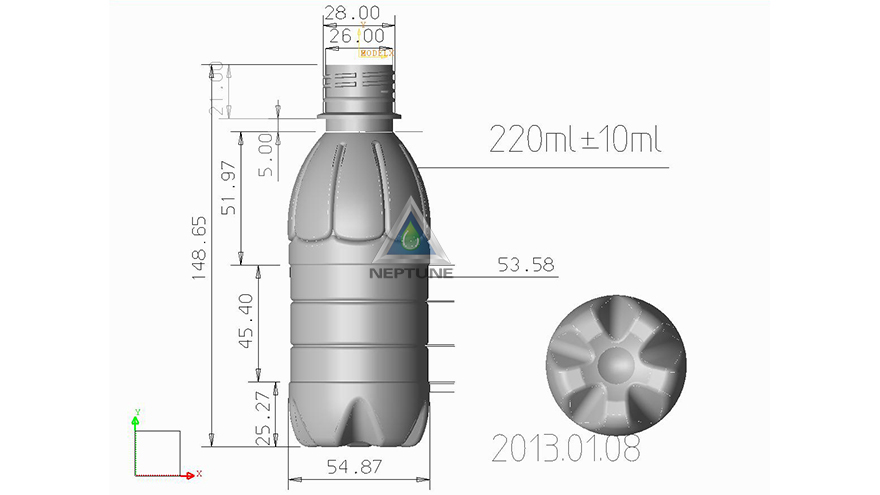
Production Capacity: 2000 bottles per hour while produce 220 ml bottle
500ml Bottle
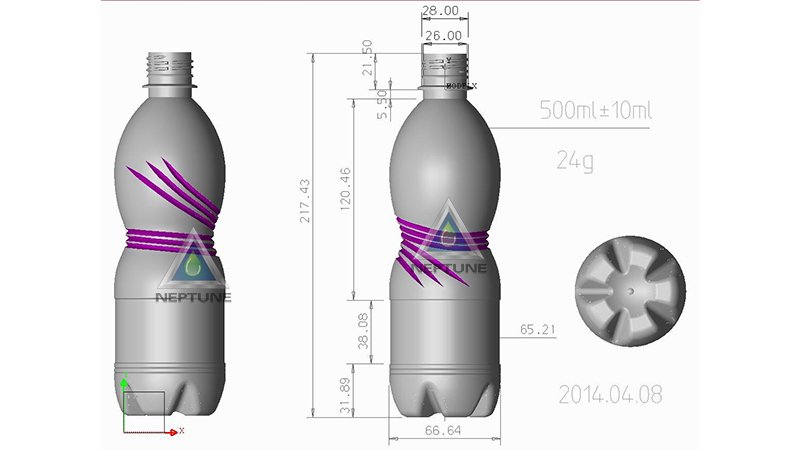
Production Capacity: 2000 bottles per hour while produce 500 ml bottle
500ml Bottle
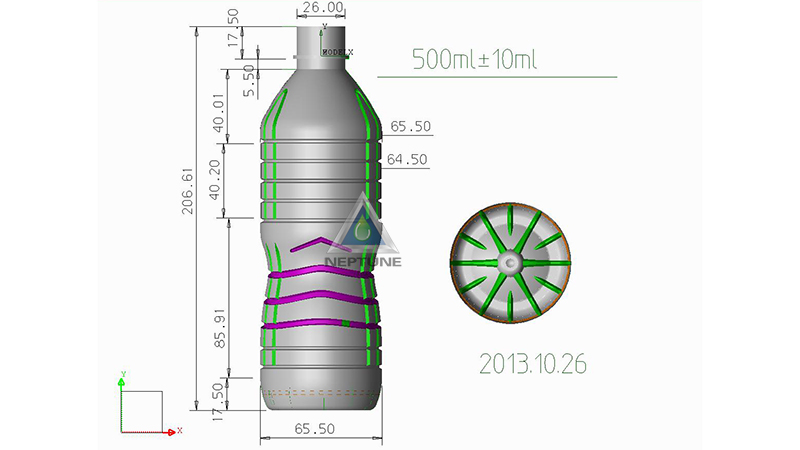
Production Capacity: 2000 bottles per hour while produce 500 ml bottle
750ml Bottle
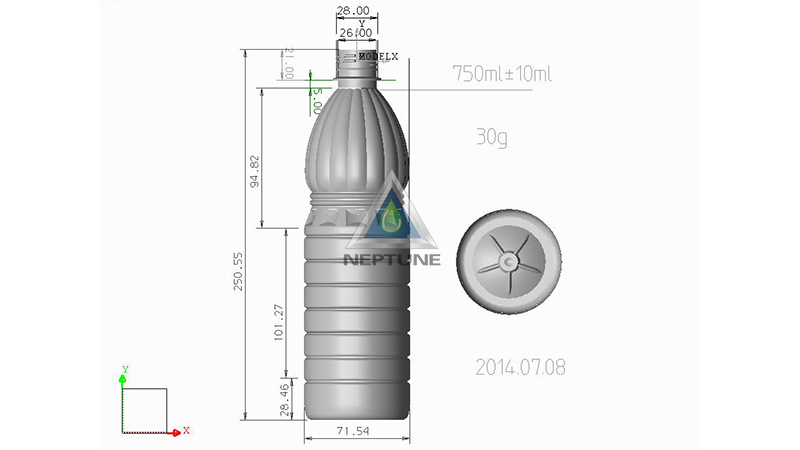
Production Capacity: 1600 bottles per hour while produce 750 ml bottle
1500ml Bottle
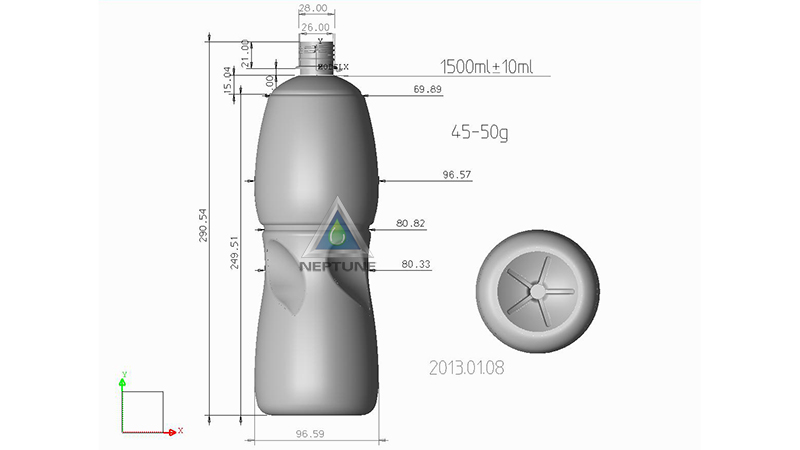
Production Capacity: 1300 bottles per hour while produce 1500 ml bottle
2000ml Bottle
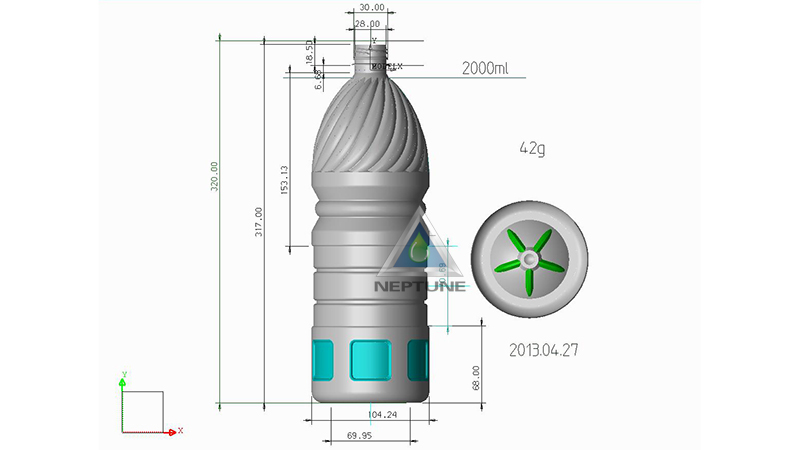
Production Capacity: 1000 bottles per hour while produce 2000 ml bottle
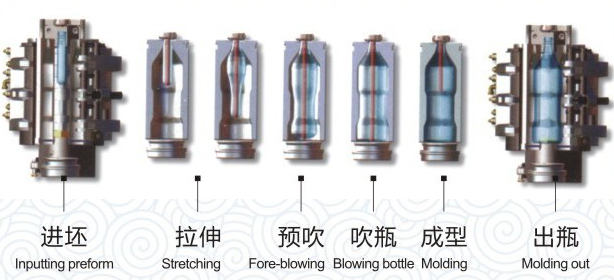
2000BPH Automatic PET Bottle Blow Molding Machine is a flexible and efficient solution for manufacturing plastic PET bottles. By changing the blow mold, you can produce bottles of different volumes and shapes. The machine allows for customization of bottle thickness, shape, and volume according to your requirements. Here are some sample production capacities for reference:
For more detailed information and specific inquiries, please contact NEPTUNE MACHINERY.
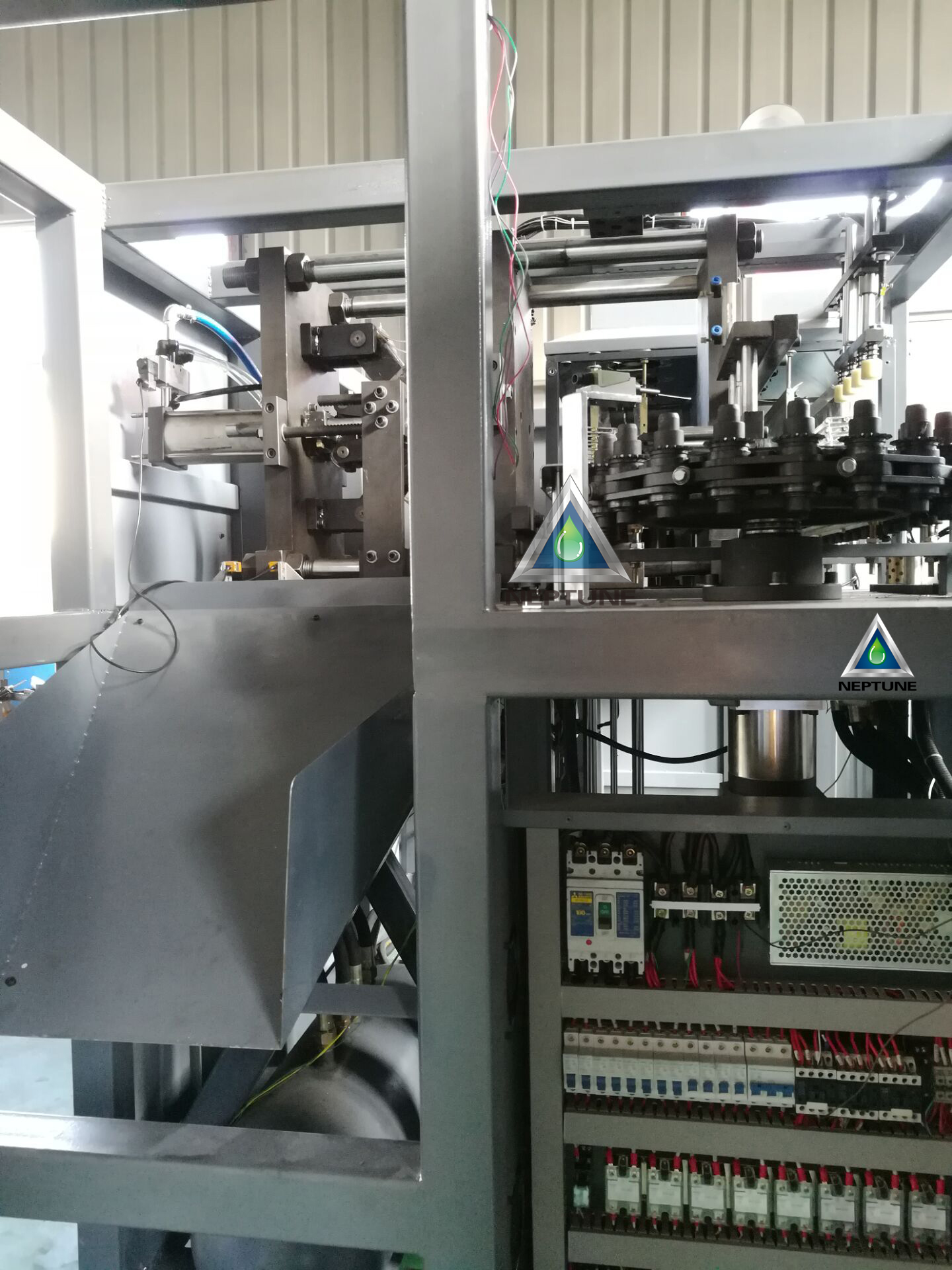
Elevate your PET bottle manufacturing process with the NEPTUNE Machinery 2000BPH Automatic PET Bottle Blow Molding Machine. Contact us today to explore how this advanced solution can enhance your production capabilities.
- Efficiency: Swift and efficient production with a high output rate.
- Versatility: Accommodates various bottle sizes to meet market demands.
- Precision: Ensures precision in molding for consistent, high-quality bottles.
- User-Friendly: Designed for easy mold changes and minimal downtime.
- Global Support: Oversea installation support for a seamless setup.
Fully automatic
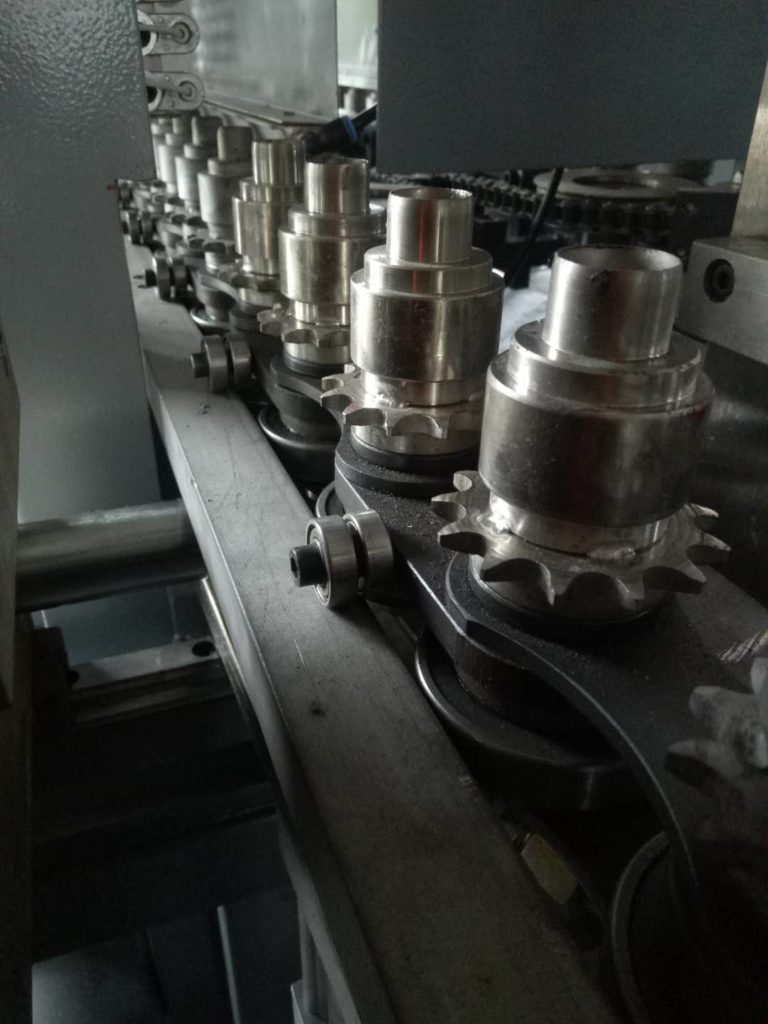
The process you described outlines the key steps in the production of PET bottles using an automatic PET bottle blow molding machine. Here’s a breakdown of the steps:
- Automatic Loading of Preform:
- The preforms, which are essentially small, tubular-shaped plastic pieces, are loaded into the machine’s preform loading system.
- Automatic Conveyor to Heating:
- The preforms are conveyed to a heating system. This system typically uses infrared heaters to bring the preforms to the ideal temperature for the blowing process.
- Automatic Heating of the Preform:
- The preforms undergo controlled heating to reach the required temperature. This is a critical step to ensure the preforms are malleable and can be properly blown into the desired bottle shape.
- Automatic Sending of Preform to Blowing:
- Once heated, the preforms are automatically transferred to the blowing station of the machine.
- Automatic Blowing of Plastic Bottle:
- The preforms are stretched and blown using high-pressure air to take on the shape of the mold, transforming them into plastic bottles. This is the actual blow molding process.
- Automatic Conveyor to Air Conveyor Outlet System:
- After the blowing process, the newly formed plastic bottles are conveyed to the air conveyor outlet system. This system is designed to seamlessly connect with the filling machine, creating a continuous and efficient production line.
- Connection with Filling Machine:
- The air conveyor outlet system ensures a smooth connection between the blow molding machine and the filling machine. This connection facilitates the seamless transfer of bottles for the filling process in the next stage of production.
By automating these steps, the production process becomes highly efficient, reducing labor requirements and ensuring consistent quality in the manufactured PET bottles.
Why choice BM-A2 blow molding machine ?
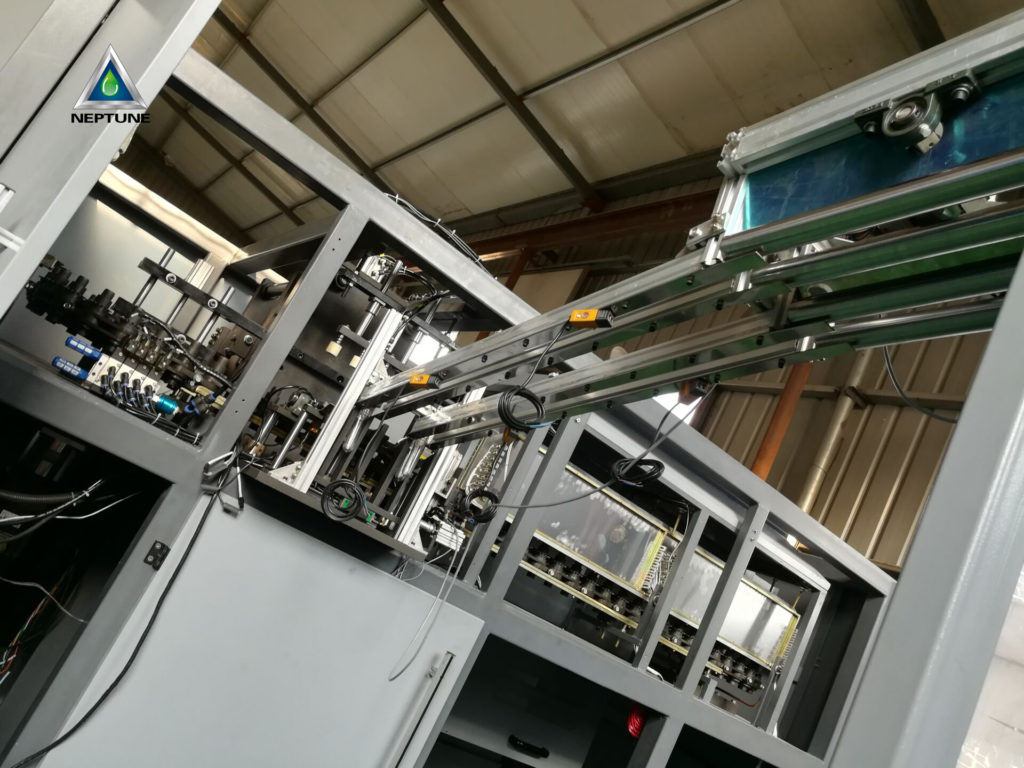
2000BPH Automatic PET Bottle Blow Molding Machine is extensively used for producing hollow plastic containers of various sizes. It boasts several key features that contribute to its efficiency and reliability:
- Stable Product Quality: The machine is designed to ensure consistent and stable quality of the produced plastic containers.
- Compact Design: With a small footprint, the machine is space-efficient, making it suitable for various manufacturing setups.
- Low Energy Consumption: It is designed to be energy-efficient, contributing to cost savings and environmental sustainability.
- Ease of Operation: The machine is user-friendly, featuring easy operation and convenient maintenance.
- High-Quality Spare Parts: All spare parts undergo advanced treatments and precise machining, meeting high technical standards.
- Advanced Bearings and Guide Rails: Moving parts are equipped with boundary lubricating bearings and straight guide rails, enhancing durability and reducing mechanical noise.
- Famous brand Components: The machine incorporates Japanese-made components, such as guiding blocks and bumpers, ensuring reliability and longevity.
- High Output Rate: The air blowing mechanism is uniquely designed to achieve a very high output rate of finished products.
- Computer-Controlled Operation: The operation of the machine is computer-controlled, ensuring accuracy and reliability in the manufacturing process.
- Human-Machine Interface (HMI): The machine features an HMI that allows for individualized operations and real-time monitoring, enhancing overall efficiency and control.
Overall, the 2000BPH Automatic PET Bottle Blow Molding Machine is a sophisticated and efficient solution for plastic container production, combining advanced technology with user-friendly features. Its reliable performance makes it an excellent choice for manufacturers seeking high-quality and high-output bottle production.
How Does the Bottle Blow Molding Machine Work?
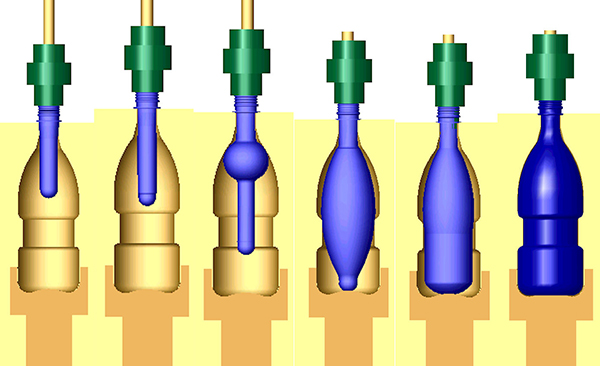
2000BPH Automatic PET Bottle Blow Molding Machine involves several key steps in the bottle production process:
- Preform Heating:Special preform heaters are used to heat the PET preforms to the required temperature. This heating process makes the preforms malleable for the subsequent stretching and blowing stages.
- Opening of the Blow Mould:The blow mould is opened by the closing unit, creating space for the insertion of the preheated PET preform.
- Insertion of the Preform:The preheated PET preform is inserted into the open blow mould.
- Closing of the Blow Mould:Once the preform is properly positioned in the mould, the blow mould is closed, securing the preform in place.
- Bottle Stretching and Blowing:The stretching and blowing process begins, during which the preform is stretched and shaped to conform to the contours of the mould, resulting in the formation of the final bottle shape.
- Opening of the Mould and Bottle Transport:After the stretching and blowing process is complete, the blow mould is opened. The finished bottle is then transported to the exit conveyor.
- Bottle Prepared for Transport:The completed bottle is prepared for transport, and it moves along the conveyor to the next stage in the production or packaging process.
This sequence of steps highlights the continuous and automated nature of the blow molding process. The machine’s ability to seamlessly execute these steps contributes to its efficiency in producing PET bottles with consistent quality.
Video of 2000bph bottle Blowing making machine
Fall down outlet bottle way
It is just automatic fall down plastic bottle.
Air conveyor outlet bottle way
It can connect with air conveyor system so that easy conveyor plastic bottle to filling machine by air fan.