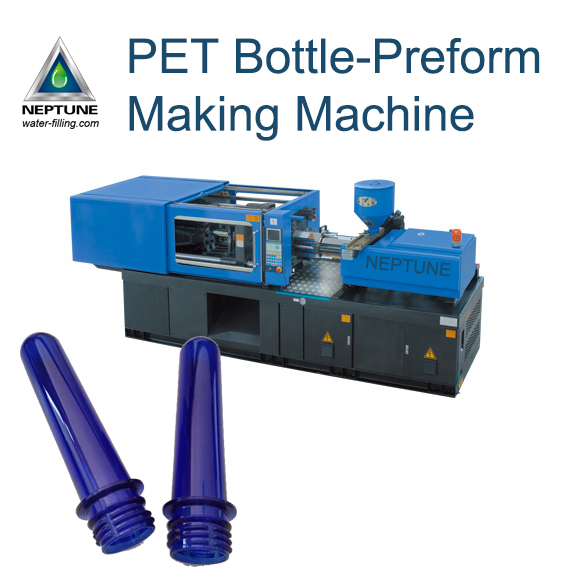
Fob Price $ 23,500.00
What this price included?
- 100T Injection Molding Machine
- PET Plastic Dryer
- Auto Loader
- Preform Mold
- Plastic Crusher
- Air Mold-Chiller 3HP
Bottle preform making machine is a specialized piece of equipment designed for the production of preforms, which are the initial forms of plastic bottles before they are blown into their final shape. This machine is an essential part of the plastic bottle manufacturing process and is commonly used in the beverage industry for producing bottles for water, soft drinks, and other liquid products.
Here are some key features and aspects of bottle preform making machines:
- Injection Molding Process:Bottle preform making machines utilize the injection molding process, where molten plastic material is injected into a mold to create the shape of the preform.
- Material Compatibility:These machines are typically designed to work with specific types of plastic materials, with PET (Polyethylene Terephthalate) being a common choice for beverage bottles.
- Mold Design:The molds used in these machines are designed to produce preforms with the desired shape and dimensions based on the requirements of the final bottle.
- Heating and Cooling Systems:The machines include heating elements to melt the plastic material and cooling systems to solidify the molded preforms.
- Automation and Control:Modern bottle preform making machines often feature automated processes and computerized control systems to ensure precision and efficiency in the production process.
- Output Capacity:The production capacity of these machines is determined by factors such as the number of cavities in the mold, the cycle time, and the overall efficiency of the machine.
- Integration with Bottling Lines:The preforms produced by these machines are later heated and blown into the final bottle shape as part of the complete bottling production line.
- Customization:These machines can be configured and customized based on specific requirements, including the design, size, and production volume of the bottles.
- Quality Control:Stringent quality control measures are implemented to ensure that the produced preforms meet the required standards in terms of dimensions, weight, and consistency.
In summary, a bottle preform making machine plays a crucial role in the plastic bottle manufacturing process by producing the preforms that serve as the starting point for creating final bottles through the blow molding process.
Capacity of production | 2300 psc depend on 18gram preform |
Injection Ton | 100 ton |
Mold cavity | 4 Cavity |
what a complete PET Bottle-Preform Making Machine included?
1. 100T Injection Molding Machine
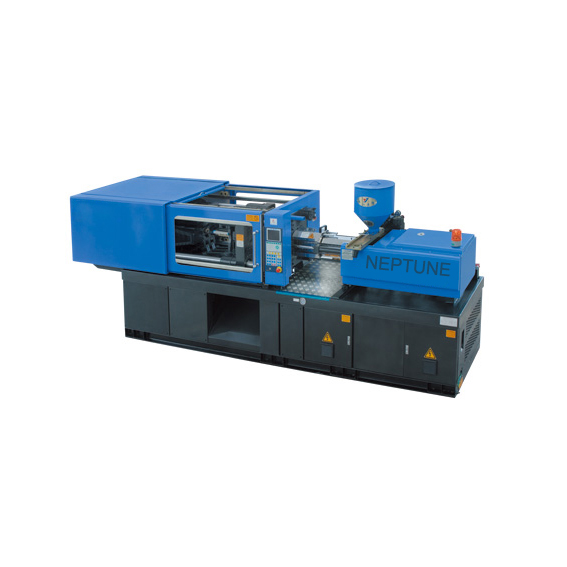
1) All computer control system
2) Super silence hydraulic circuit
3) High speed and high-pressure injection, ideal for high precision and thin-walled molding products
4) Real-time injection process curve display
5) Enlarged clamping stroke to meet with larger stroke requirements
6) 4-stage of injection speed, 3-stage of holding pressure, 4-stage of metering phase can be setup according to products’ requirements
7) Optimal platen design, with toggle junction casting together with platen improves rigidity of mechanical system hence improves product dimensions accuracy
8) Screw and barrel are made of high quality new materials, which extended their working lif
9)All hydraulic components and seals are from famous international manufacturers
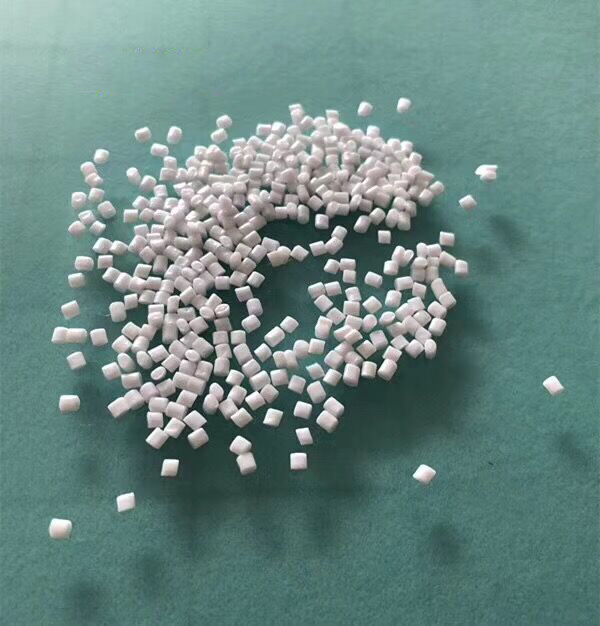
2. PET Plastic Dryer
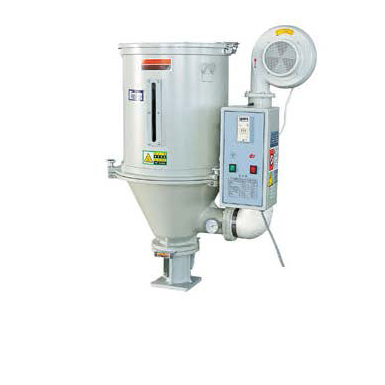
Well-distribute Heated Wind The heat efficiency is high enough to shorten great amount of drying time. Precise Temperature Controls The precise temperature controls ensure and keep a high accuracy of temperature. Save Time and Manpower As the hopper body and bottom are designed separately, and therefore it is very convenient to clean materials and quite simple and quick to renew materials as well. The Trustworthy Design Fine exterior,solid construction.Short material-melting time greatly helps to promote the spouting speed.
3. Auto Loader
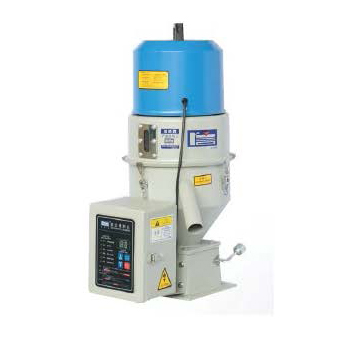
The main engine and the material hopper are designed separately,and thus it is safe,easy and convenient to be opperated.
The whole operation is controlled by MicroTrip computer.
Equipped with an independent filter,which is very convenient to clean up dust.
The equipped muffler reduces the noise in operation.
Stainless steel material hopper is light in weight,durable and very convenient for cleaning the device.
The control box,being designed separately,is easy to be well maintained.
Auto-buzzer will give alarm while lacking material.
Auto-protective device protects motor against overloading.
4. Preform Mold
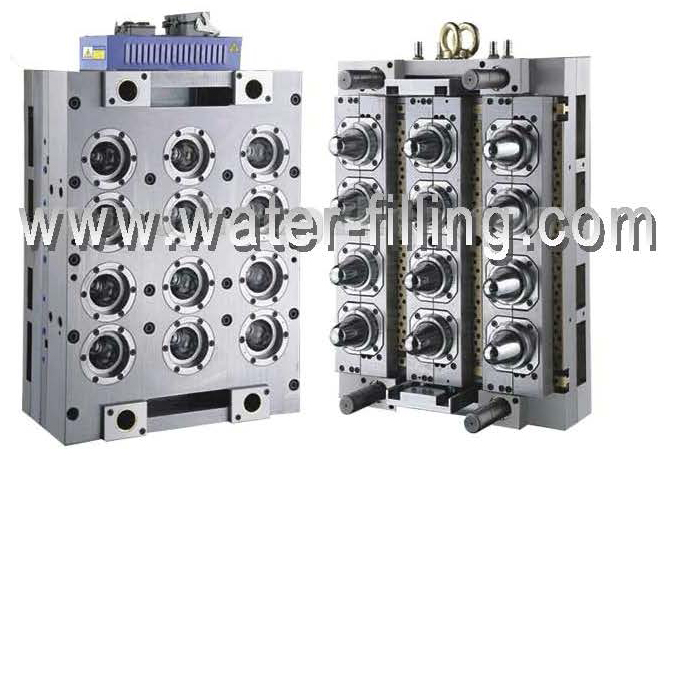
Preform tensile tests using computer simulation designed to ensure blowing success rate.
- Using the world forward two double taper positioning technology, each cavity independent self-locking, concentricity ≤ 0.08mm.
- The mold cavity, core selection Sweden and Germany imported mirror plastic mold steel corrosion resistance, high hardness, long life.
- Threaded ports according to international standards, imported nitrided steel, high hardness, long life.
- Runner advanced design, single-point nozzle temperature, heating temperature, improve the quality of preform.
- Excellent cold room temperature water cooling system to achieve high efficiency, fully automated production.
- Free scissors gate, ensuring automatic production mold, reduce workers’ labor.
- Mould life of at least 300 million times die times.
- Runner using PID control system, which is characterized by automatic repair and automatic protection function, prolong the service life of electric devices;
- Temperature control within 1 degree, sure to avoid being burned material within the hot runner is occurring, can yield more than 99%;
- New nozzle design makes it easier to mold maintenance, parts ejector nozzle, heating parts, insulated part, and the thermocouple without removing the case easy to replace mold, helps to reduce downtime and saving maintenance costs.
5. Plastic Crusher
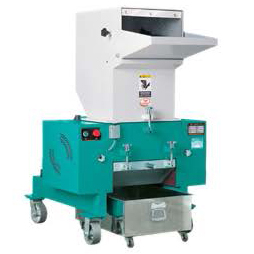
6. Air Mold-Chiller 3HP
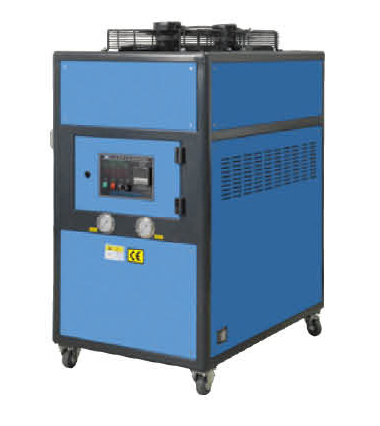
The equipment can fast cooling the blow mold, greatly raise the working efficiency of blow moding machines and obviously improve the bottle quality.
How Does An Preform Making Machine Working ?
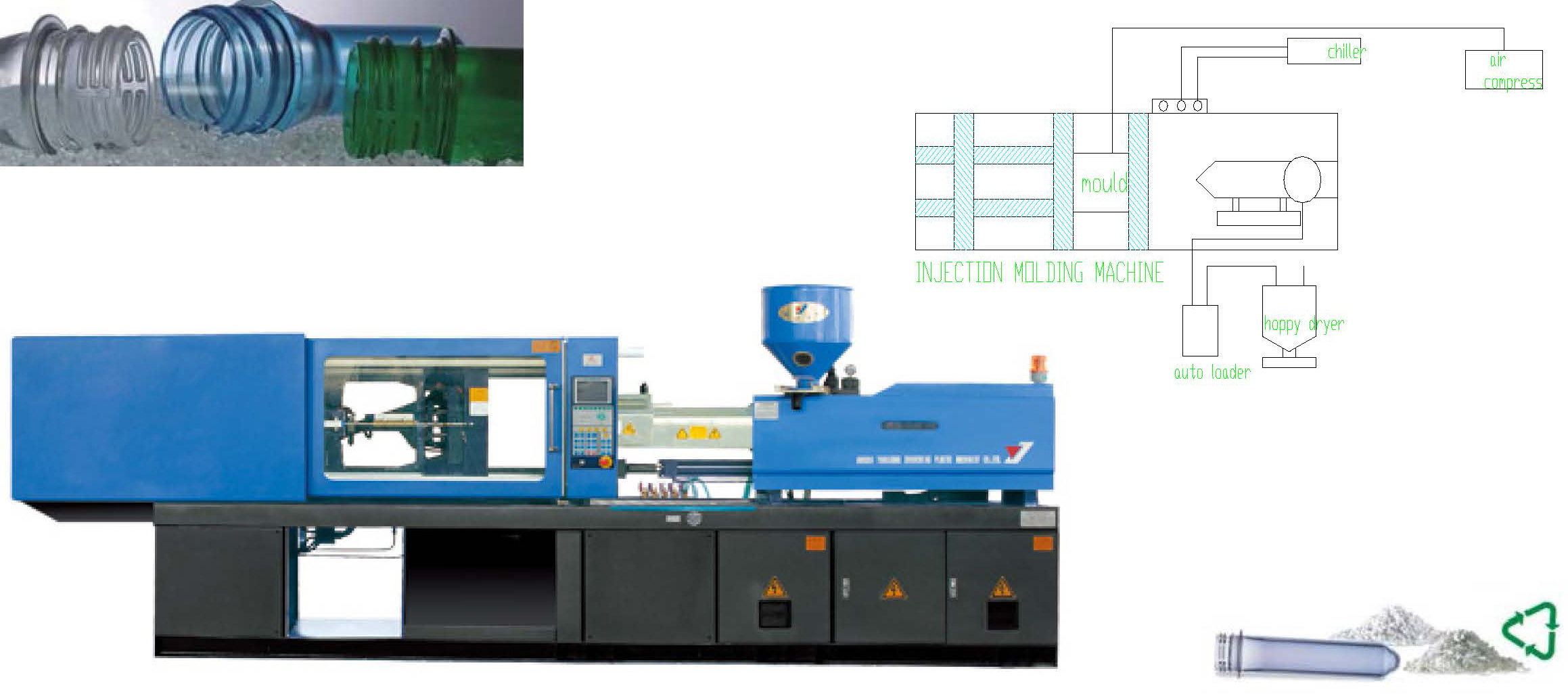
Flow chart of the injection molding process for producing preforms:
- Plastic Material Selection:
- Begin with the selection of the appropriate plastic material for the preform. Commonly used materials include PET (Polyethylene Terephthalate).
- Dehumidification:
- Ensure that the plastic material is dehumidified to eliminate any moisture, which could affect the quality of the preform during the injection process.
- Material Loading:
- Load the dehumidified plastic material into the hopper of the injection molding machine. The hopper stores and feeds the material into the injection unit.
- Injection Machine:
- The injection molding machine consists of an injection unit and a clamping unit. In the injection unit, the plastic material is heated and melted. The molten plastic is then injected into a mold.
- Mold Filling:
- The molten plastic is injected into the mold cavity under high pressure. The mold is designed to shape the plastic into the desired preform form.
- Cooling and Solidification:
- The injected plastic material cools and solidifies within the mold, taking the shape of the preform.
- Mold Opening:
- After the plastic has solidified, the mold opens to reveal the formed preform.
- Ejection:
- The preform is ejected from the mold using ejector pins.
- Inspection:
- Inspect the preforms for quality, ensuring they meet the specified standards.
- Packaging:
- Once inspected and approved, the preforms are ready for packaging. They can be stored for future use or transported to the next stage in the production process.
This flow chart outlines the key steps in the injection molding process for producing preforms. Each step is crucial in ensuring the quality and consistency of the final product.
The injection molding machine used for preform making comes with several advantages, contributing to its efficiency and reliability in the plastic bottle manufacturing process:
- Double Mold Adjusting Motors:
- Equipped with double mold adjusting motors, ensuring steady and smooth operation during mold adjustment.
- Optimum Mold Design:
- Designed with an optimum oblique ranked five-points supporting curved rib and cabinet-type mold, enhancing stability and efficiency in the molding process.
- Self-Regulating Support:
- The movable mold board utilizes self-regulating support, protecting the drawbar and extending its lifespan. This feature also ensures smooth and steady mold locking.
- Double Injection-Advancing Hydro-Cylinders:
- The double injection-advancing hydro-cylinders guarantee a steady and smooth injection process, preventing deformation of the fixed mold board.
- Hydraulic System with Double Scaling:
- The hydraulic system adopts pressure-flow double-scaling to control oil channels. International famous brand hydraulic elements are used, and the machine is designed with reasonable oil lines, ensuring smooth and steady operation.
- Double-Cylinder Balanced Injection:
- The machine features double-cylinder balanced injection, screw rods, material tubes, non-step, large-torque hydraulic motor, adjustable speed control, and adjustable back pressure. This combination allows it to meet the requirements of various plastics to be injected and shaped.
These advantages collectively contribute to the reliability, precision, and efficiency of the injection molding machine in the production of preforms, providing a foundation for the subsequent stages in the bottle manufacturing process. The incorporation of advanced features and technologies enhances the overall performance and quality of the preform-making machine.
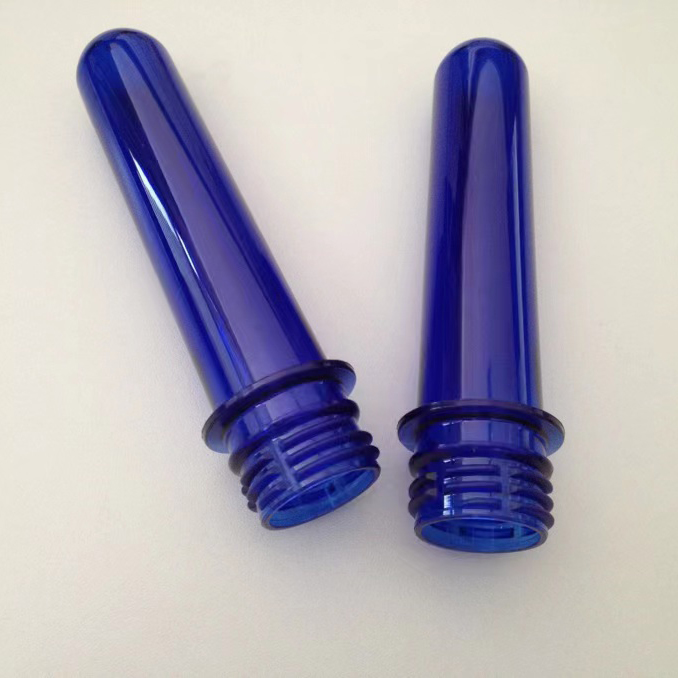
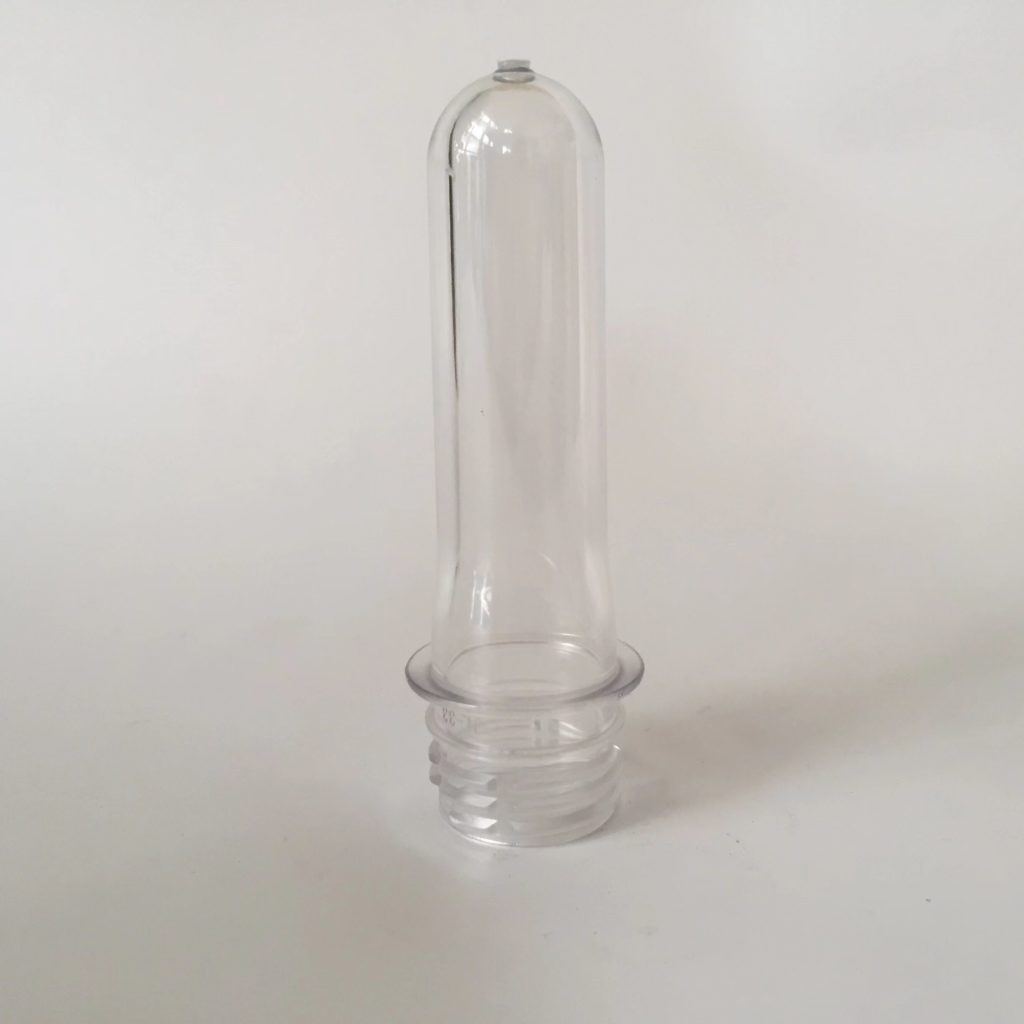
FAQ
warranty & Aftersales
Warranty 1 year if not human being damage, all-life aftersales, we still have a lot over 10years customer buy spare part from us.
Dilivery time
30Days production time. If specilly voltage will delay 1week to buy specilly electricity element
Installation and Tranning
China engineer aboard install and tainning.
Payment Safety
All quote trade term is FOB. Benifit account name is SHENZHEN NEPTUNE MACHINERY CO.,LTD. Make sure your payment is safe. We will not change our bank account name and account by any reason.
shipment
All payment is not included shipment cost because shipping cost is change frequency by ship every week.
We can help you check shipment cost recently week. And booked ship container.
We will respossible all China freight and clear export process and cost.