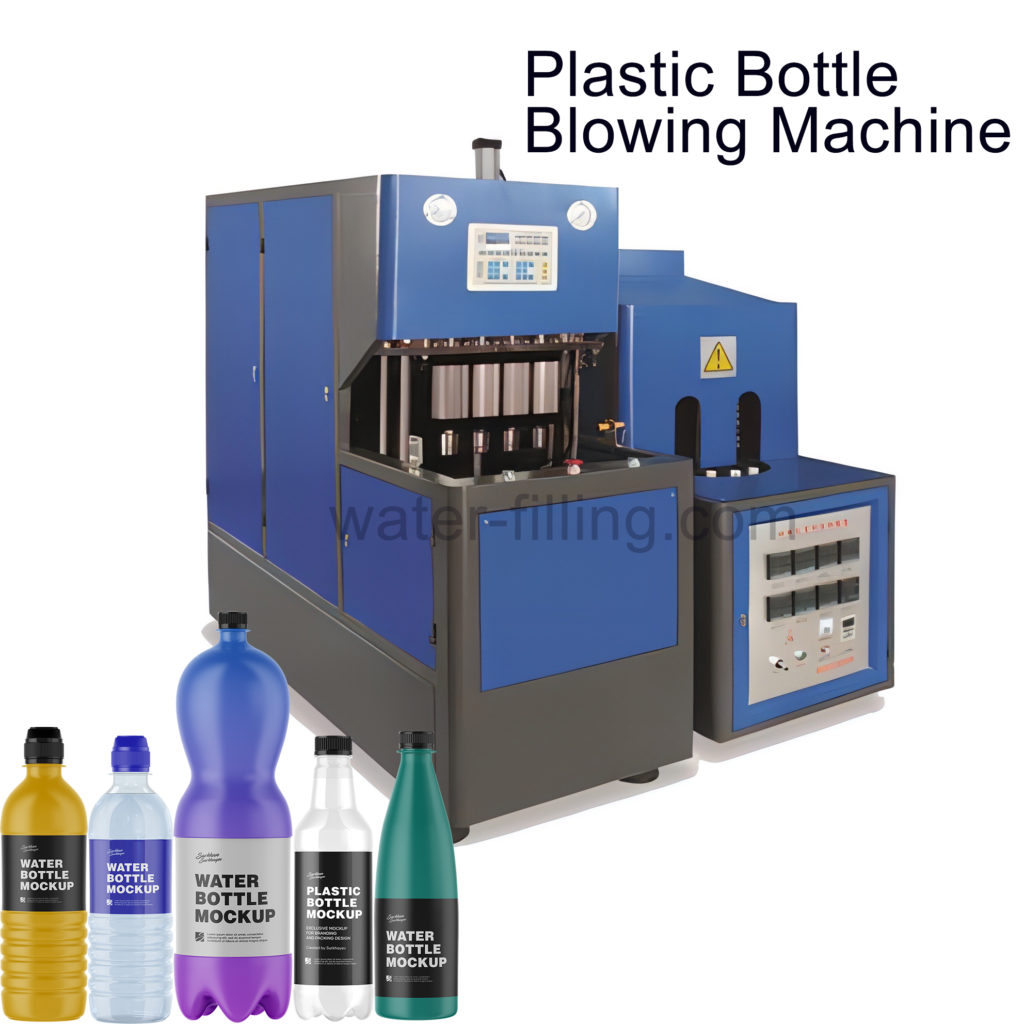
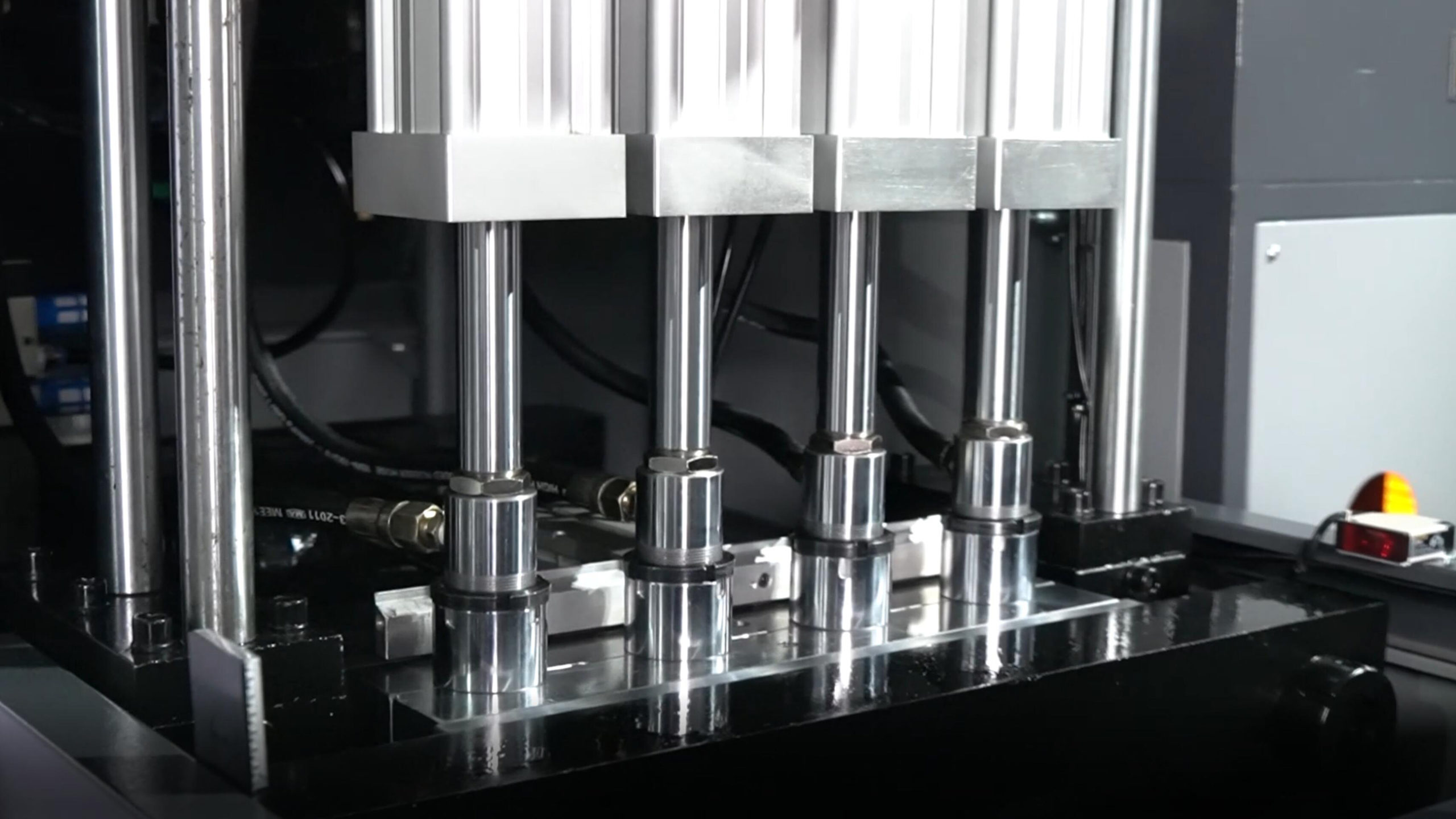
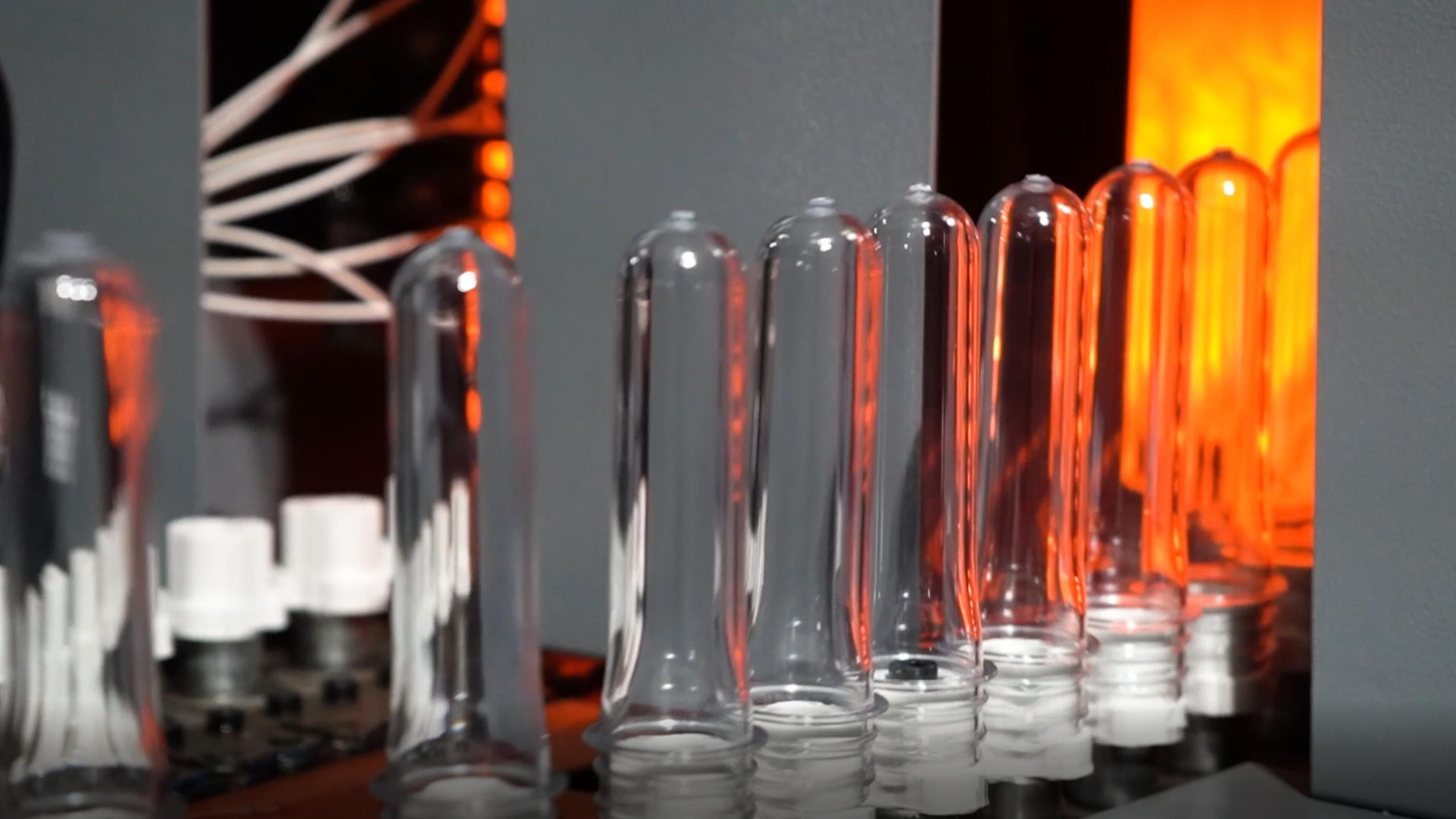
Bottle blowing machine for production plastic pet bottle for sport drink, mineral water, purified water and vitamin water bottle package.
WHAT IS THE BOTTLE BLOWING MACHINE COST?
FOB PRICE $ 13,700.00
What this price included?
1 | BM-4 4Cavity Blow Shaping Machine | 1 SET |
2 | Rotating oven; | 1 SET |
3 | HP & LP Air compressor; 1.5M3/min 30KG | 1 SET |
4 | 0.6m3 Air Tank | 1 SET |
5 | Refrigeration Air Dryer; 1.0M3/3.0Mpa | 1 SET |
6 | Air filter 1.5m3/min 30KG | 2SET |
7 | 4Cavity blow mold (200-2000ml) | 1SET |
8 | Mold Air-Cooling (Cooling the mold to make sure machine continued running) | 1SET |
9 | Spare part | 1SET |
2000BPH PLC control Semi-Automatic 4-cavity bottle blowing machine is a rapid and efficient solution for producing plastic water bottles. Here’s an overview:
- High Production Speed:This machine is designed to achieve a production speed of 2000 bottles per hour, making it a fast and efficient option for PET container manufacturing.
- Semi-Automatic Operation:The machine operates in a semi-automatic mode, indicating that certain processes are automated while others may require manual intervention. This balance allows for efficient production while maintaining control over key steps.
- 4-Cavity Design:The machine features a 4-cavity design, enabling it to simultaneously produce four plastic bottles in each cycle. This multi-cavity capability contributes to increased productivity.
- PLC Control:The machine is equipped with Programmable Logic Controller (PLC) technology. PLC control enhances the precision and efficiency of the production process, ensuring accurate and consistent bottle production.
- Automatic Bottle Falling System:The automatic fall-down bottle system eliminates the need for manual handling by workers to remove the plastic bottles. This not only improves operational efficiency but also enhances workplace safety.
- Energy-Saving and Small Size:The machine is designed with energy-saving features, contributing to reduced operational costs. Its compact size makes it suitable for facilities with space constraints.
- Versatile Application:The machine is versatile and can produce plastic containers for various industries, including food, medicine, cosmetics, pesticides, chemicals, and beverages.
- Quick Return on Investment (ROI):Due to its high production speed and efficient design, the machine offers a fast return on investment, making it a financially attractive option for businesses.
In summary, the 2000BPH PLC control Semi-Automatic 4-cavity bottle blowing machine combines speed, efficiency, and automation, making it an ideal choice for plastic water bottle manufacturing across different industries.
Technical Parameter of 4 cavity bottle blowing machine
Product material | PET Preform |
Volume | 200ml to 1000ml |
Theoretical output | 2500PCS/H |
Preform length | 55mm-150mm |
Preform inner diameter | Φ20mm-30mm |
Max. mould plate Dimension (L x W) | 460×330×160MM |
Max. mould thickness | 180mm |
Clamping force | 45KN |
Mould opening stroke | 160mm |
Main machine (L x W x H) | 1660x820x2150MM |
Main machine weight | 1000Kg |
Heater (L x W x H) | 2160x580x1350 |
Heater weight | 300Kg |
Power | 26kw |
raleted Machine
Video of the fast 2500BPH water bottle blowing machine
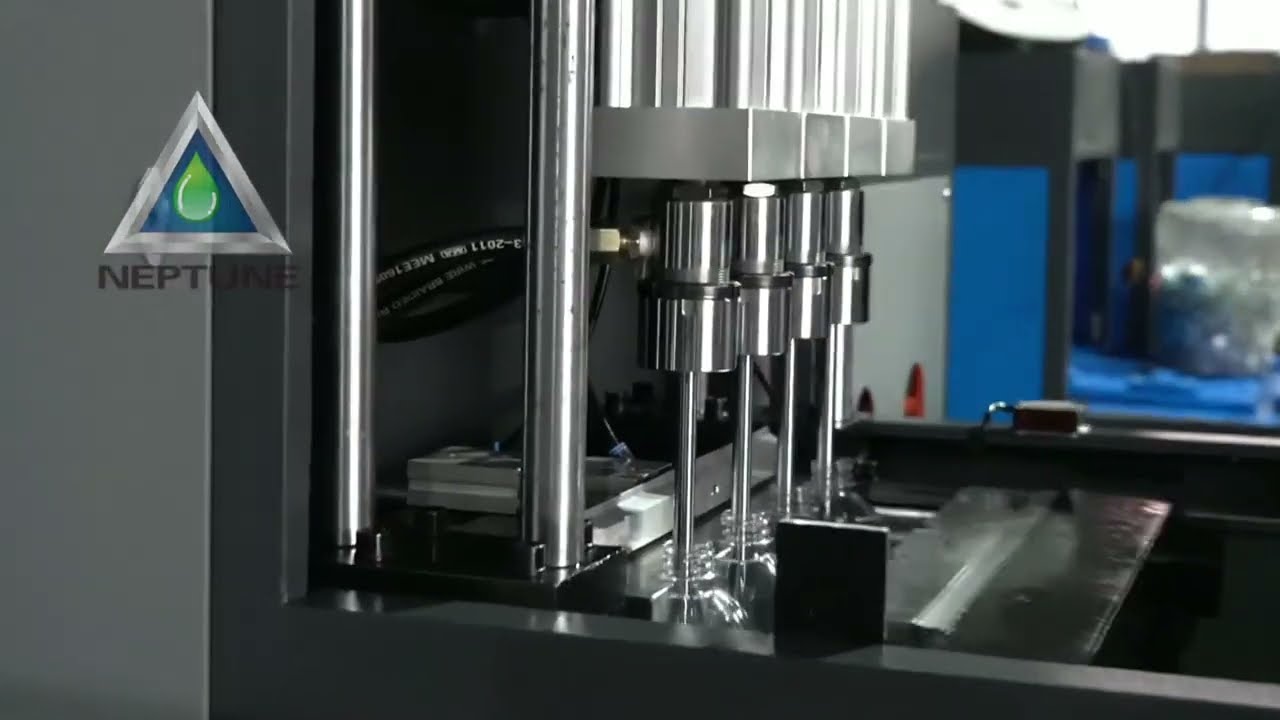
Before bottle blowing machine leaving NEPTUNE factory, every water bottle blowing machine undergoes a rigorous ex-factory test conducted by NEPTUNE to ensure the highest quality. This meticulous testing process guarantees that each machine meets the required standards and operates flawlessly. The ex-factory test is a crucial step in delivering a product that not only meets but exceeds customer expectations.
By conducting a meticulous ex-factory test, NEPTUNE aims to deliver water bottle blowing machines that not only meet industry standards but also embody a commitment to quality craftsmanship and customer satisfaction. This process reflects NEPTUNE’s dedication to providing reliable and high-performance equipment for bottle manufacturing businesses.
Key Aspects of the Ex-Factory Test:
- Quality Assurance:The primary objective of the ex-factory test is to assure the quality of each water bottle blowing machine. This involves thorough inspections of components, mechanisms, and overall construction to identify and rectify any potential issues.
- Performance Evaluation:NEPTUNE conducts comprehensive performance evaluations during the test. The machine’s ability to produce high-quality plastic bottles at the specified speed and precision is thoroughly examined to ensure optimal functionality.
- Functional Testing:Each function and feature of the machine is tested individually and collectively. This includes evaluating the heating process, mold adjustment, bottle stretching, blowing, and other critical operations.
- Precision and Accuracy:The precision and accuracy of the machine in producing bottles of consistent quality are carefully assessed. This ensures that the final products meet industry standards and customer requirements.
- Safety Checks:Safety is a top priority. NEPTUNE conducts thorough safety checks to ensure that the machine operates safely for both workers and the production environment. Emergency shutdown systems and other safety features are rigorously tested.
- Durability and Reliability:The durability and reliability of the water bottle blowing machine are put to the test. The machine is subjected to simulated continuous production to assess its long-term performance and reliability under real-world conditions.
- User-Friendly Interface:The user interface and controls are evaluated for user-friendliness. NEPTUNE ensures that the machine is easy to operate, with intuitive controls and clear indications for monitoring and adjustment.
- Documentation Review:All documentation, including manuals and guides, is reviewed to confirm its completeness and clarity. This ensures that end-users receive comprehensive guidance for the installation, operation, and maintenance of the machine.
Once Produce 4psc Bottle, Bottle Automatic Fall Down
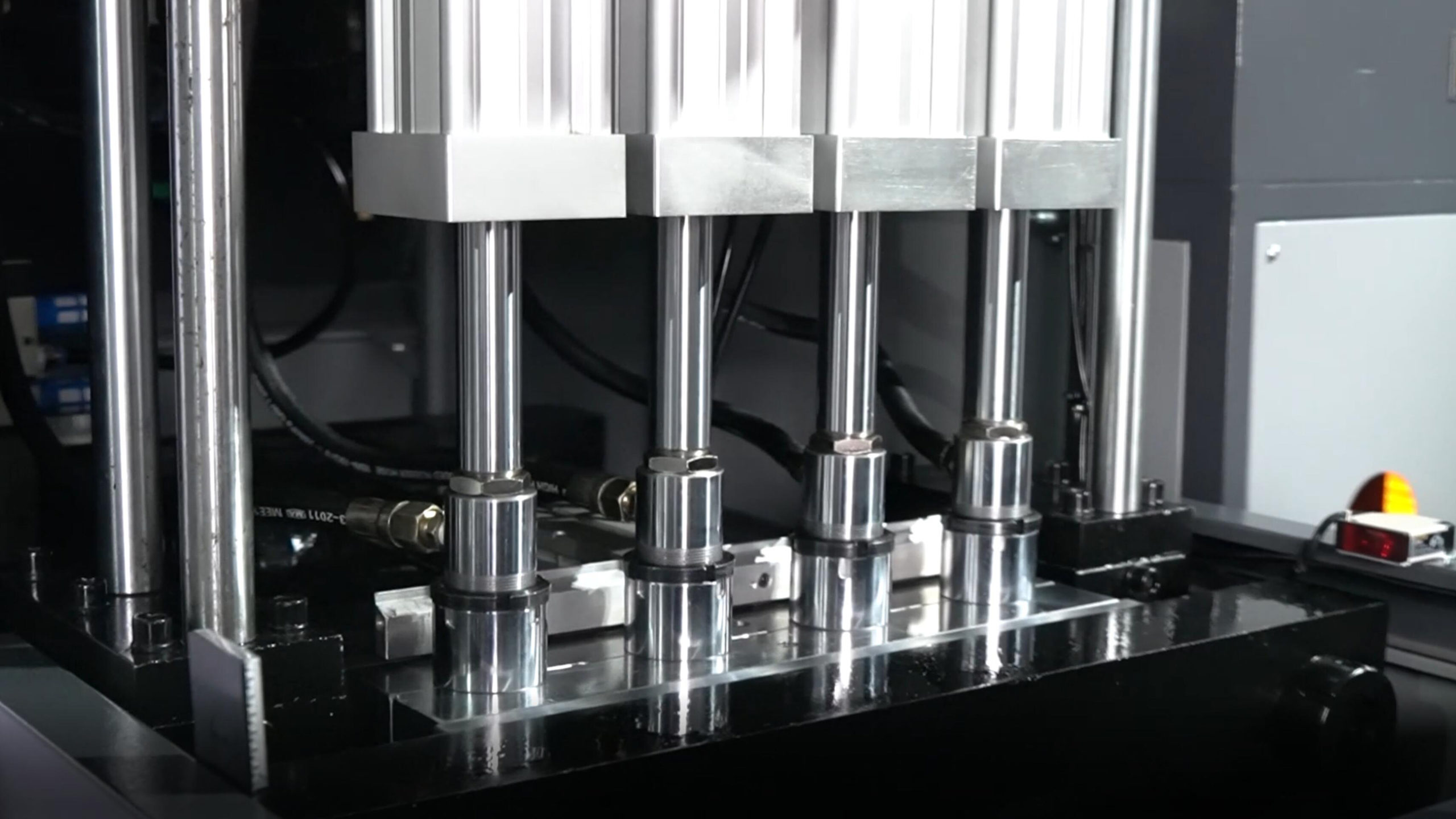
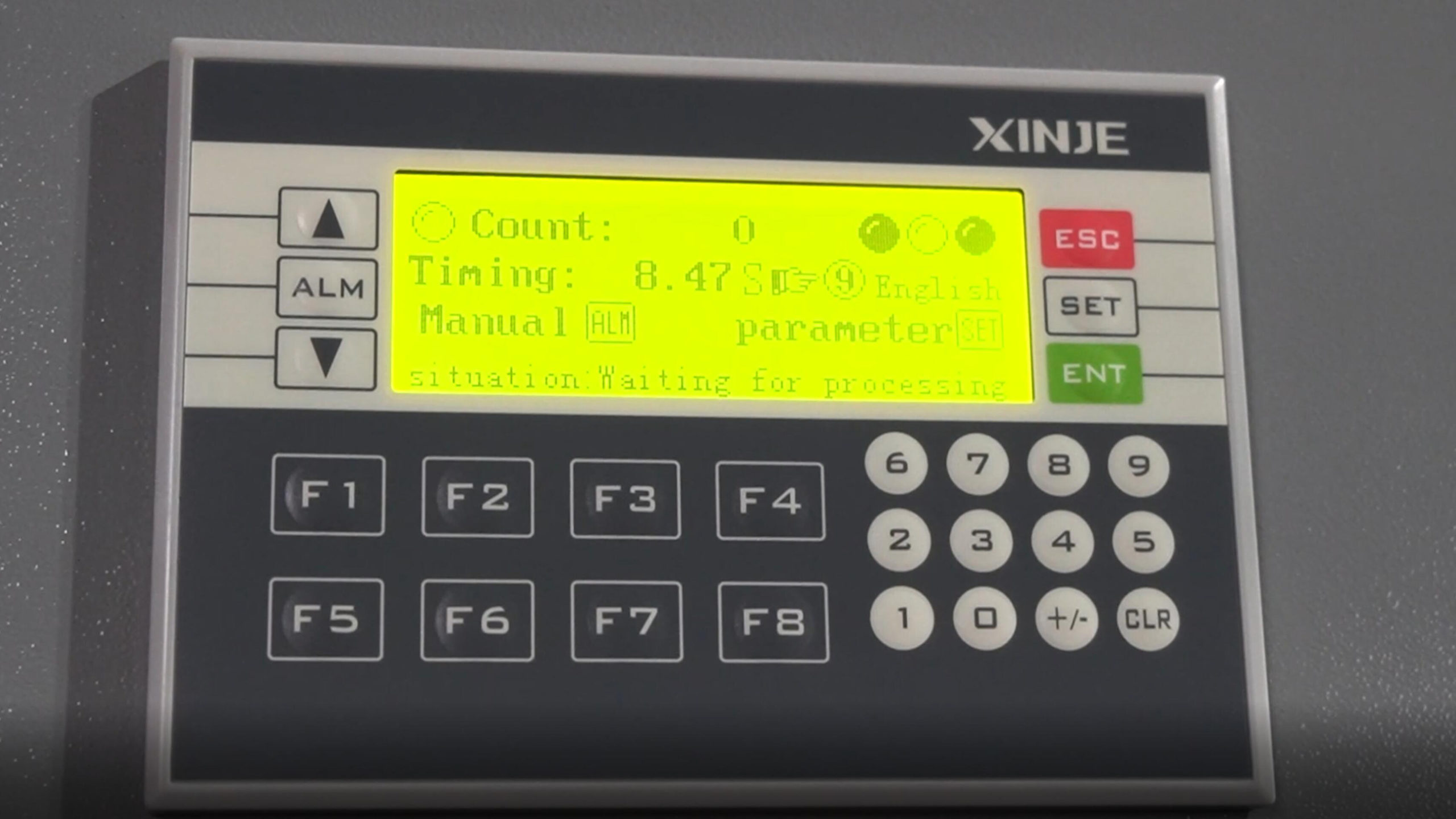
2000BPH PLC control Semi-Automatic 4-cavity bottle blowing machine by NEPTUNE incorporates an innovative automated falling system for seamless handling of produced bottles. This advanced feature streamlines the production process and eliminates the need for manual intervention, enhancing efficiency and reducing labor requirements.
- Efficient Multi-Cavity Production:The machine is equipped with a 4-cavity design, allowing it to produce four plastic bottles simultaneously. This multi-cavity production capability significantly increases overall output.
- Synchronization with Production Cycle:As the machine completes the blowing process for a set of four bottles, the automated falling system is synchronized to release the bottles in a controlled manner. This ensures that the falling process aligns seamlessly with the production cycle.
- Precision and Consistency:The automated falling system is designed for precision and consistency. It ensures that each bottle falls in a predictable manner, preventing any disruptions or potential damage to the bottles during the descent.
- Continuous Production Workflow:With the automated falling system in place, the production workflow remains continuous. As one set of bottles is released, the next set is already in the process of being formed, allowing for uninterrupted production.
- Elimination of Manual Handling:Unlike traditional methods where operators manually remove bottles from the machine, the automated falling system eliminates the need for such manual handling. This not only reduces labor requirements but also minimizes the risk of errors or accidents.
- Enhanced Operational Efficiency:The integration of an automated falling system enhances the overall operational efficiency of the bottle blowing machine. It contributes to a smoother production process, reducing downtime between cycles.
- Safety Considerations:The automated falling system is designed with safety in mind. Protective measures are in place to ensure the safe release of bottles without posing any risk to operators or the production environment.
What Is Materials Of Blow Molding Machine ?
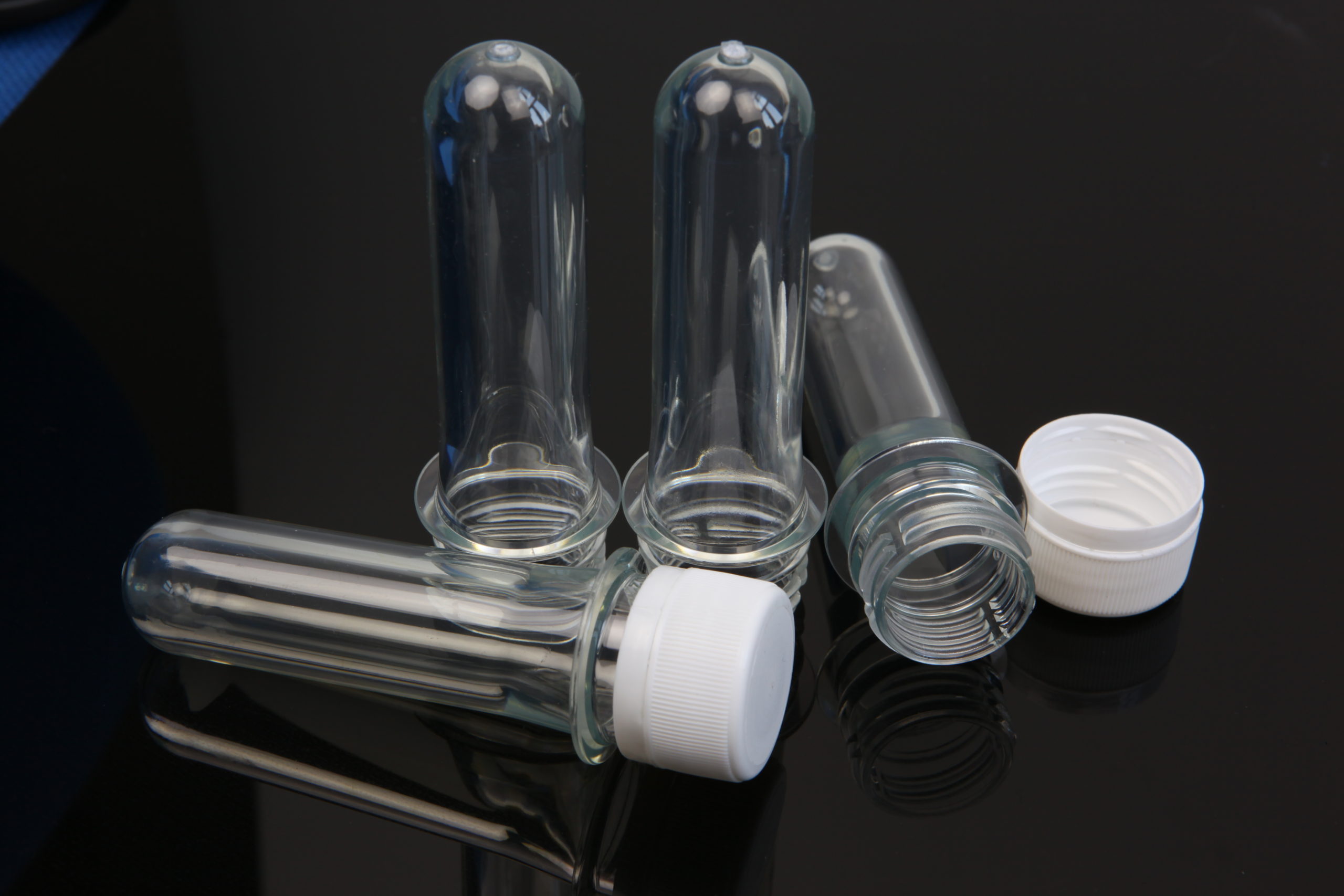
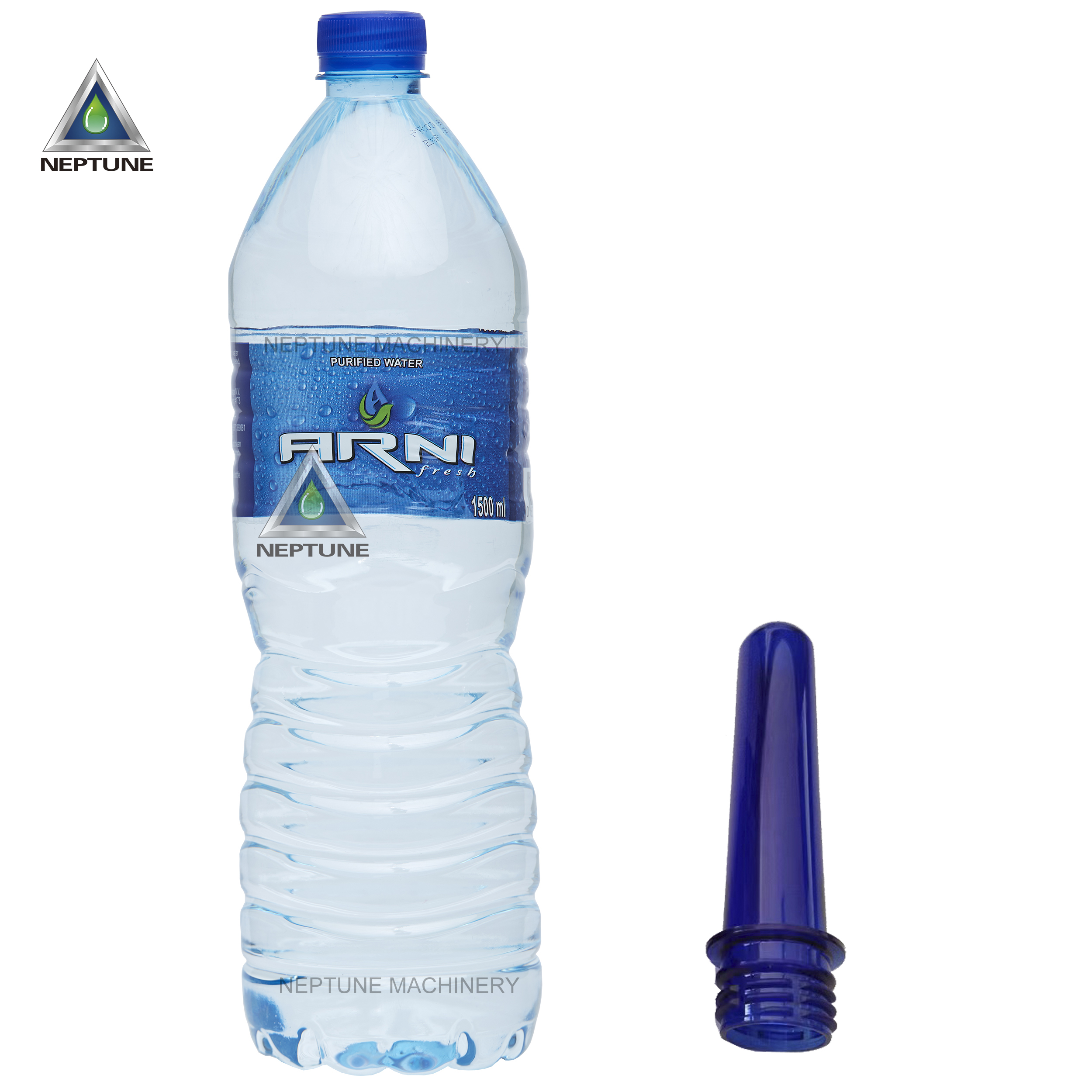
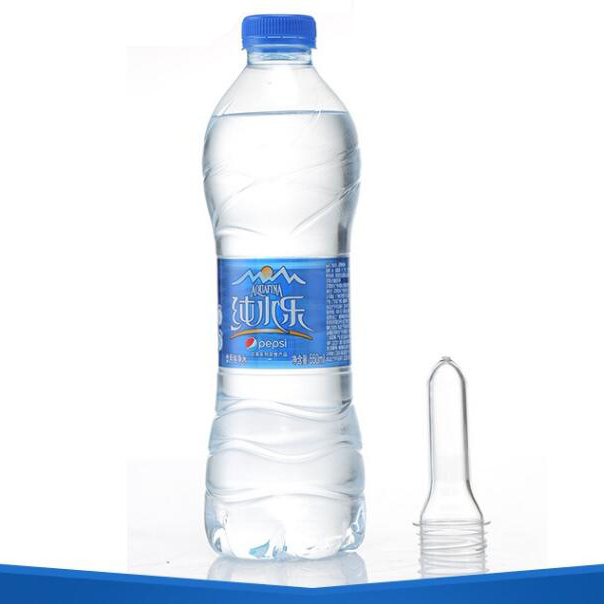
Overview of Preforms
1. Preform Definition:A preform refers to the initial form or shape of a plastic bottle before it undergoes the process of blow molding. It is produced through injection molding, where molten plastic is injected into a mold to create a small, strong, and compact form.
2. Production Process:Preforms are manufactured using injection molding machines, which are specialized equipment for creating intricate plastic shapes. Injection molding involves injecting molten plastic into a mold cavity, where it solidifies into the desired shape.
3. Cost and Complexity: Injection molding machines are relatively expensive, and the production process requires technical expertise. Due to the complexity and cost, many bottled water companies choose to purchase preforms from specialized injection molding facilities.
4. Packaging and Transportation:Preforms are compact and durable, allowing for efficient packaging. Typically, a box can contain 500 preforms, and large quantities can be transported in containers, making them suitable for shipping and storage.
5. Advantages of Using Preforms:
- Cost-Effectiveness: Buying preforms can be more cost-effective for companies that don’t have the resources or expertise for in-house injection molding.
- Efficient Packaging: The small size and strength of preforms facilitate efficient packaging, reducing storage space requirements.
- Reduced Freight Costs: As preforms are compact and lightweight, they incur lower freight costs compared to transporting finished plastic bottles.
6. Challenges in Freight of Plastic Bottles:Weight and Volume: Plastic bottles, being lightweight and voluminous, can lead to higher freight costs. Additionally, the susceptibility to damage during transportation poses a challenge.
Conclusion:The use of preforms in plastic bottle production offers a practical solution for companies looking to streamline the manufacturing process. By leveraging the advantages of preforms, businesses can achieve cost savings, efficient packaging, and reduced freight expenses compared to transporting finished plastic bottles.
Whole Blow Molding Machine Running Process
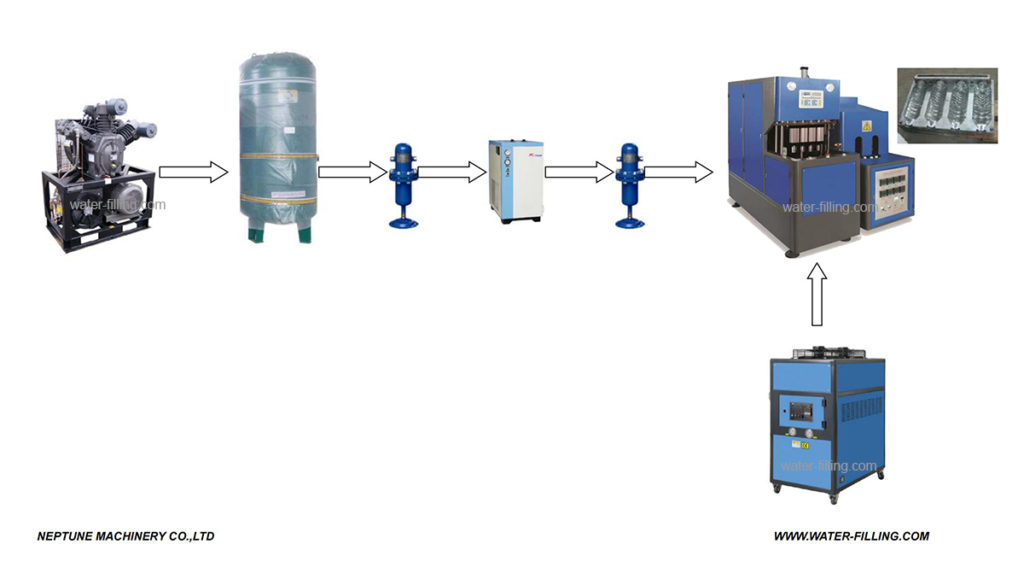
Benefits of the Auxiliary Equipment:
- Air Quality Assurance:The combination of air filler, air dryer, and air filter ensures that the compressed air used in the bottle blowing process is of high quality, free from impurities and moisture.
- Operational Stability:The air tank helps in stabilizing air pressure, contributing to the overall stability of machine operation. Consistent air pressure is essential for achieving uniform and reliable bottle blowing.
- Prevention of Contamination:The emphasis on air quality control not only enhances the performance of the machine but also prevents any contamination of the plastic bottles during the blowing process.
- Efficient Mold Cooling:The mold-cooling system plays a crucial role in maintaining an optimal temperature for the molds, ensuring prolonged operational efficiency and preventing overheating.
2000BPH PLC control Semi-Automatic 4-cavity bottle blowing machine by NEPTUNE is accompanied by essential auxiliary equipment that plays a crucial role in ensuring optimal performance, safety, and product quality. Here’s a brief overview of the key auxiliary components:
- High-Pressure Air Compressor:The high-pressure air compressor is a fundamental component that provides the necessary compressed air for both the bottle blowing process and machine operation. It ensures a reliable and consistent supply of high-pressure air.
- Air Tank for Air Storage:To maintain air pressure stability, an air tank is incorporated into the system for storing compressed air. This helps in preventing fluctuations in air pressure during the production process.
- Air Filler and Air Dryer:The air filler and air dryer are crucial elements for maintaining the cleanliness and quality of the compressed air. The air filler removes impurities, while the air dryer eliminates moisture from the compressed air, preventing contamination of the plastic bottles.
- Air Filter After Air Dryer:Following the air dryer, an additional air filter is introduced to further refine the quality of the compressed air. This ensures that the air used in the bottle blowing process is free from contaminants that could affect the final product.
- Mold-Cooling System:The mold-cooling system is implemented to address the temperature concerns associated with prolonged machine operation and mold usage. It helps in cooling the mold efficiently, particularly in hot weather conditions, contributing to consistent production quality.
NEPTUNE’s attention to auxiliary equipment underscores its commitment to delivering a comprehensive and reliable bottle blowing solution with a focus on air quality, operational stability, and product integrity.
How Do The Blow Molding Machine Work?
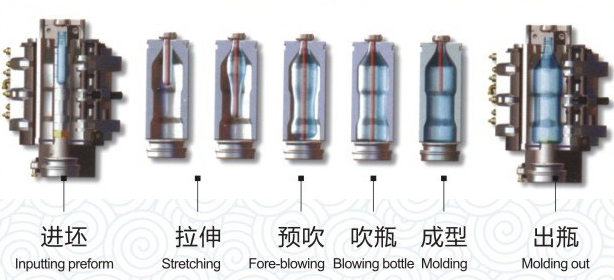
Working of the Semi-Automatic Plastic Bottle Blowing Machine:
1. Preform Insertion:Workers manually insert preforms into the heating oven. Preforms are the initial forms of plastic bottles and are shaped through injection molding.
2. Heating Process:The inserted preforms go through a heating process in the oven. Heat is applied to the preforms to bring them to the ideal temperature for the subsequent blowing process.
3. Transfer to Blowing Machine:Once the preforms are adequately heated, they are transferred to the semi-automatic blowing machine. This machine is designed to blow air into the preforms to expand and shape them into the final plastic bottle.
4. Blowing Process:A worker operates the machine, initiating the blowing process. The machine uses air pressure to blow into the preforms, causing them to expand and take the shape of the mold within the machine.
5. Mold Determination:The shape of the plastic bottle is determined by the mold used in the machine. Different molds can be employed to produce bottles of various shapes and sizes.
6. Semi-Automatic Operation:The term “semi-automatic” indicates that while certain steps, such as preform insertion and operation initiation, are manual, the blowing process itself is automated. The machine assists in shaping the plastic bottles efficiently.
7. Final Bottle Formation:As a result of the blowing process, the preforms transform into fully formed plastic bottles. These bottles are then ready for further processing, such as filling with water or other beverages.