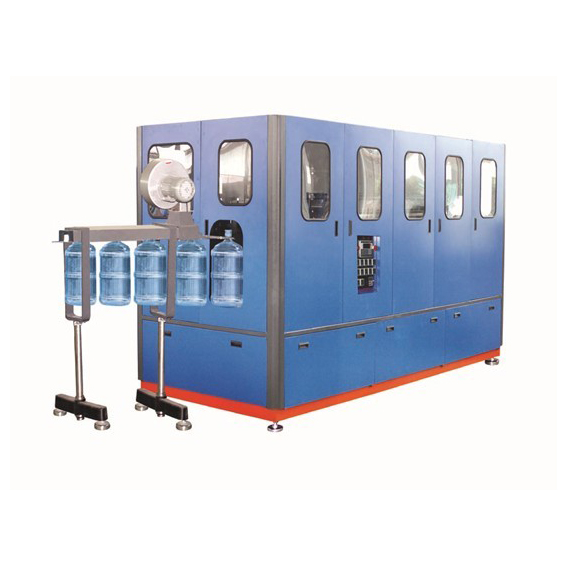
NEPTUNE BM-120A 5-Gallon PET Bottle Blowing Machine
FOB PRICE $ 40700
What this price included?
No | Description of Goods | model no |
1 | 5 GALLON automatic blowing machine | BM-120A (1-cavity) |
2 | High pressure compressor | 3.9M3/MIN |
3 | Air storage tank | 0.6M3 |
4 | Air filters*2SET | 3.0M3/MIN |
5 | Air cooling dryer | 3.0M3/MIN |
6 | BLOW MOLD | 1CAVITY |
7 | Mold-chiller | 3HP |
8 | spare parts |
NEPTUNE – Your Complete Solution for Reliable and Efficient 5 Gallon PET Bottle Production
NEPTUNE BM-120A is a fully-automatic jar bottle blow molding machine designed for producing 3 to 6-gallon PET plastic bottles used in bottling mineral water or purified water. With a production capacity of 120 to 180 bottles per hour, this machine is ideal for businesses seeking efficient and reliable bottle production. The PET plastic bottles it produces are robust and reusable.
Key Features:
- Volume of Product: 10-19L (3-5 gallons)
- Production Capacity: 120-180 bottles per hour
- Connection Compatibility: The machine comes with a bottle conveyor, allowing seamless connection with filling, capping, and washing machines.
Advantages of Automatic Reuse Bottle Blow Molding Machine:
- Labor Cost Savings: The automatic design reduces the need for manual labor, contributing to cost savings.
- Integration with Full Automatic Line: Can be connected with the entire automatic 5-gallon bottled water production line.
Auxiliary Equipment:
- Mold chiller : Cools the mold to enhance operation speed and extend mold life.
- High-Pressure Air Compressor: Supplies air for blowing preform into plastic bottle. Also supply air for blow moding machine moving cost.
- Air Filter: Clears impurities from compressed air.
- Air Cooling Dryer: Purifies and removes moisture from compressed air.
- Air Storage Tank: Receives and supplies air for the machine as storage.
- Blow Mold: Blowing preform into bottle in the blow mold.
NEPTUNE Commitment: NEPTUNE ensures transparency by including all necessary auxiliary equipment in the quote for the blow molding machine. This approach prevents buyers from facing additional expenses later on and makes it easy to start a water bottling business seamlessly.
main Auxiliary equipment
1.High pressure air compressor
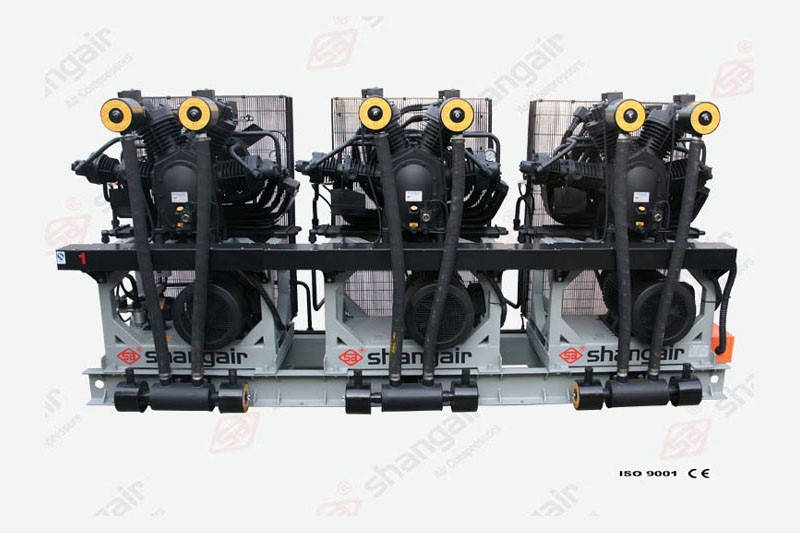
Blowing Process: During the blowing process, the compressed air is utilized to stretch and shape the heated preform into the desired bottle shape. The high-pressure air is injected into the preform, expanding it to conform to the mold cavity.
1 | Model | 3-09SH-1540T |
2 | Exhaust volume (Nm3/min) | 3.9 |
3 | Exhaust pressure (Mpa) | 4.0 |
4 | Motor power(kw) | 45kw |
5 | Weight | 1700KG |
6 | Size (LWH) | 3800×1000×1750MM |
2.Mold Chiller
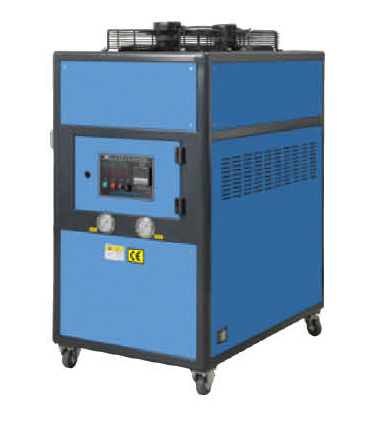
- The mold chiller is a cooling system associated with the blow mold.
- It helps maintain the temperature of the mold at an optimal level during the blow molding process.
- Cooling is essential to solidify and set the plastic material in the desired shape quickly, improving cycle times and production efficiency.
- Prevents overheating of the mold, ensuring consistent and accurate bottle formation.
In a plastic bottle maker machine, air filtration, air drying, and air storage (tank) serve essential functions to ensure the quality and efficiency of the bottle production process. Here’s a breakdown of their functions:
3.Air filter
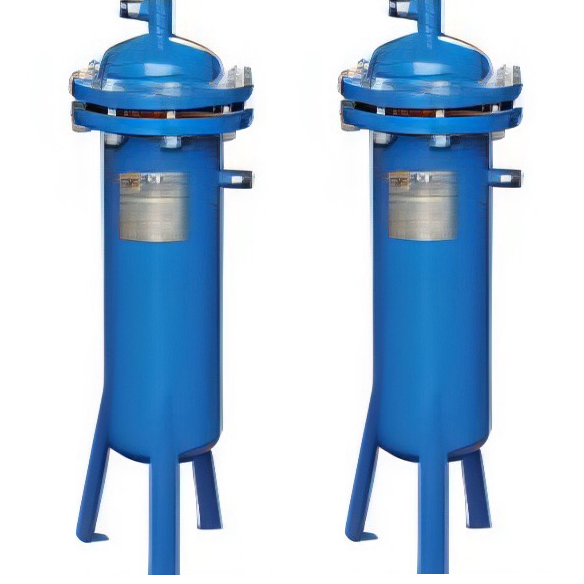
- Function: The air filter is responsible for purifying the compressed air by removing impurities, particles, and contaminants.
- Importance:
- Ensures clean and contaminant-free air, preventing damage to pneumatic components.
- Protects the quality of PET material during the preform heating and blowing stages.
- Enhances the longevity and reliability of the machine by preventing clogging and wear.
4.Air dryer
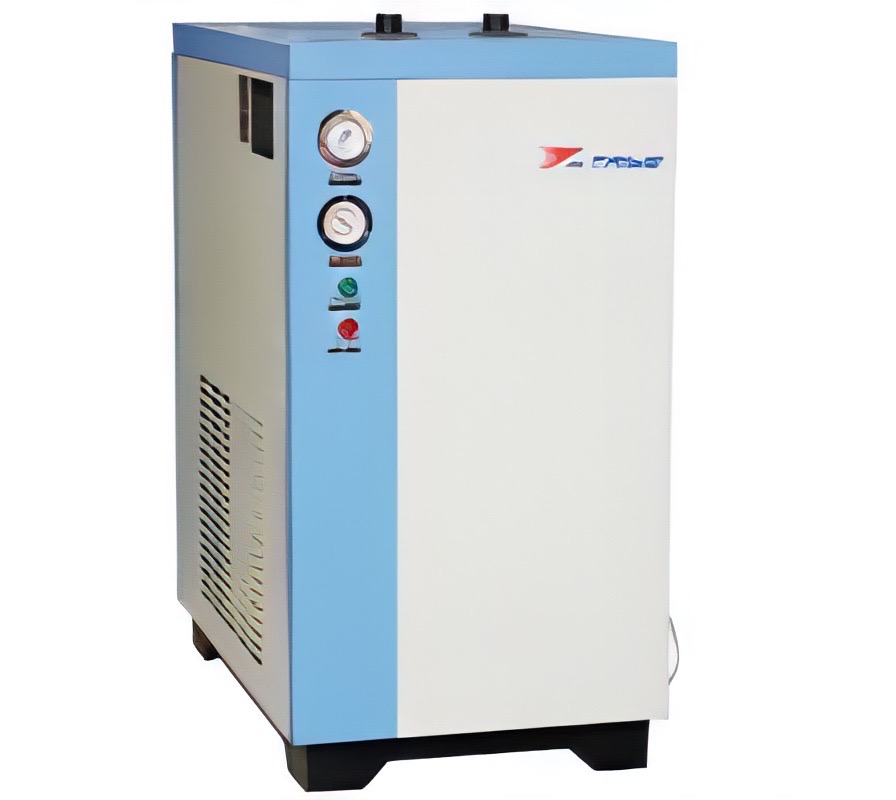
- Function: The air dryer removes moisture or humidity from the compressed air to prevent condensation.
- Importance:
- Reduces the risk of water droplets forming in the air lines, which could affect product quality and damage equipment.
- Prevents corrosion of pneumatic components, ensuring long-term reliability.
- Maintains consistent air quality, crucial for the blowing process and final product.
5.Air tank
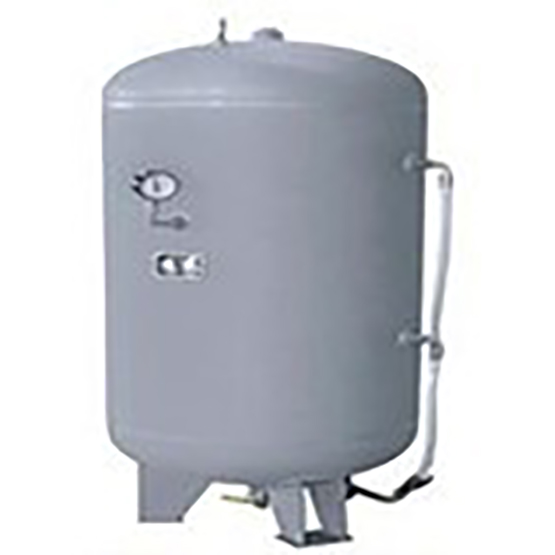
- Function: The air tank stores compressed air, providing a reservoir for immediate use during high-demand periods.
- Importance:
- Ensures a stable and consistent supply of compressed air, even during peak production.
- Helps balance air supply and demand, reducing fluctuations and maintaining optimal pressure.
- Minimizes the load on the air compressor by storing excess air during low-demand periods.
These components work together to create a reliable and efficient compressed air system for the blow molding machine, contributing to consistent product quality, equipment durability, and overall operational efficiency.
How does 5 gallon pet bottle blowing machine Working
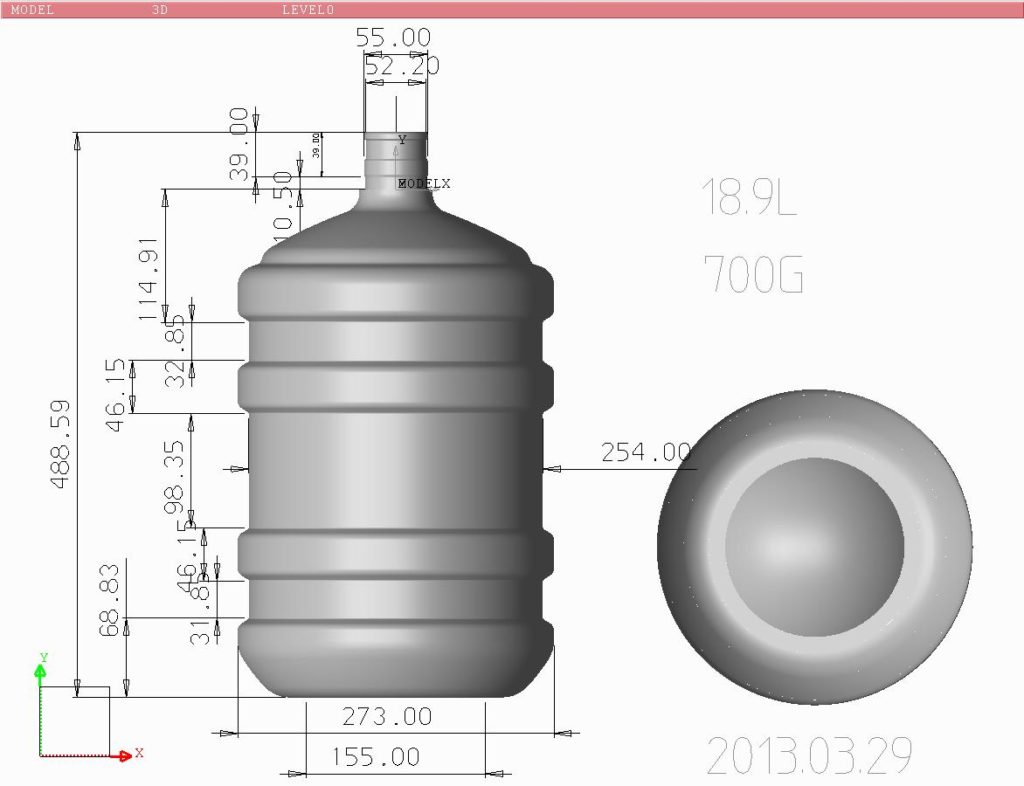
- Fully Automatic Design:
- The CM-120A is designed with full automation, including automatic loading of preforms, streamlining the production process.
- Integrated Bottle Conveyor:
- The machine comes equipped with a bottle conveyor that seamlessly connects with filling, capping, and washing machines, ensuring a continuous and efficient bottling line.
- Energy Efficiency:
- Power consumption is remarkably low at ONLY 25KW, which is 50% less than traditional machines. Over two years, the electricity savings match the machine’s cost, making it a cost-effective choice.
- PLC Control from Mitsubishi:
- The machine features PLC control from Mitsubishi, a trusted brand, and is internet-compatible, allowing for remote monitoring and control.
- Simple and Durable Design:
- The machine boasts a simple design, emphasizing durability and easy maintenance. Its simplicity ensures that it is ready for repair and can withstand the rigors of continuous operation.